For those seeking optimum performance from their PCD inserts, there are several things to take into account. Chief among them is the selection of material: tungsten carbide, ceramic, and diamond are among the most often used options, each with its own unique properties and drawbacks.
Awarded the title of most preferred material for PCD inserts, tungsten carbide offers incredible toughness and longevity, making it a fail-proof option for high-speed machining applications. Despite its advantages, it is unsuitable for endeavours that involve high vibrations due to its brittle nature.
Ceramic PCD inserts, which consist of silicon carbide, aluminum oxide, and zirconia, are renowned for their strength and robustness in high-speed machining applications. Yet due to their fragility, they should not be employed for tasks which require frequent exposure to vibration as this will cause them to become damaged.
Beholden on extreme strength and wear resistance, diamond PCD inserts are crafted from a super-hard artificial diamond material. Although the most expensive of PCD materials, these inserts demonstrate their worth in ultra-precise high-speed machining tasks that require immaculate accuracy.
PCD inserts come in numerous geometric shapes, with each design providing its own unique benefits and drawbacks. Generally, the most frequent selections are square, round, and those featuring a chamfered edge. When making your decision regarding the ideal insert for your needs, it is essential to note this diversified geometry.
Square PCD inserts are the go-to choice when it comes to machining applications. Their versatility is unmatched, as they come in several sizes to handle different tasks with ease. What’s more, their efficient cutting ability, coupled with their comfortable usage, ensures accurate results every time.
Not as commonplace as their squarish counterparts, round PCD inserts boast a remarkable array of sizes, making them perfect for various machining jobs. By affording exceptional precision and ease of use, these inserts prove to be an effective solution.
Offering accuracy and ease of use, Chamfered PCD inserts are a reliable choice for a diverse range of machining operations. As the least common type of insert, these PCD inserts can be found in a multitude of sizes to meet every project’s needs.
When selecting PCD inserts, coatings are a critical factor. From TiN, to TiCN, to TiAlN, there are numerous coatings available–each possessing advantages as well as drawbacks. Knowing which coating to select can be daunting, but understanding their benefits will prove invaluable as you decide which is the most suitable.
The market is teeming with TiN-coated PCD inserts in an array of sizes to handle all sorts of machining operations. These inserts offer precision, convenience, and ease of use, meaning they make for an ideal choice in many industrial contexts.
A wide variety of finely-crafted TiCN-coated PCD inserts are available, lending themselves to a host of machining operations. These inserts offer superior levels of precision and usability, making them the perfect choice for any project that demands accuracy. Though not as prevalent as TiN-coated inserts, they provide ample options when selecting the best insert for the job.
When it comes to inserts, TiAlN-coated PCD is the least popular option. From small to large, these inserts are suitable for numerous machining jobs and can be relied upon for accuracy. Plus, they’re user-friendly too, so you don’t have to be a machining expert to get the best results.
Before deciding on the most suitable PCD insert, the cost cannot be overlooked. With PCD inserts ranging from budget to high-end, consider what your affordability affords.
Compared to other types of inserts, Tungsten Carbide PCD inserts come at a greater cost – yet this increased price tag is justified, due to the remarkable resilience and strength of these tools.
Compared to more costly tungsten carbide inserts, ceramic PCD inserts offer a cheaper solution. However, it should be noted that they do not possess the same robustness and durability.
While the cheapest to purchase, diamond PCD inserts are comparatively fragile and lack resilience.
When it comes to picking the ideal PCD Insert, application must be regarded as one of the five vital aspects. A great range of sizes and shapes are available when it comes to these inserts so it is imperative to select the one tailored for your specific application.
Square PCD inserts are crafted specifically to meet the needs of everyday machining operations.
Specially developed, PCD-based round inserts come with specific equipment for machining.
PCD inserts configured with a chamfering are crafted to suit particular machining operations.
With so many PCD insert manufacturers out there, determining the best one can be a daunting task. But there is one factorin particular that can help you carve out the best option: reputation. Selecting a trustworthy and reliable PCD insert producer is absolutely essential if you’re after superior quality and results.
Beyond mere selection criteria, timely delivery of PCD inserts is a paramount concern. From various outlets, these sought-after inserts can be purchased, thus it is vital to take into account the duration required for receipt. To guarantee you get your order as quickly as possible, evaluate the delivery time of potential providers.
Related Product
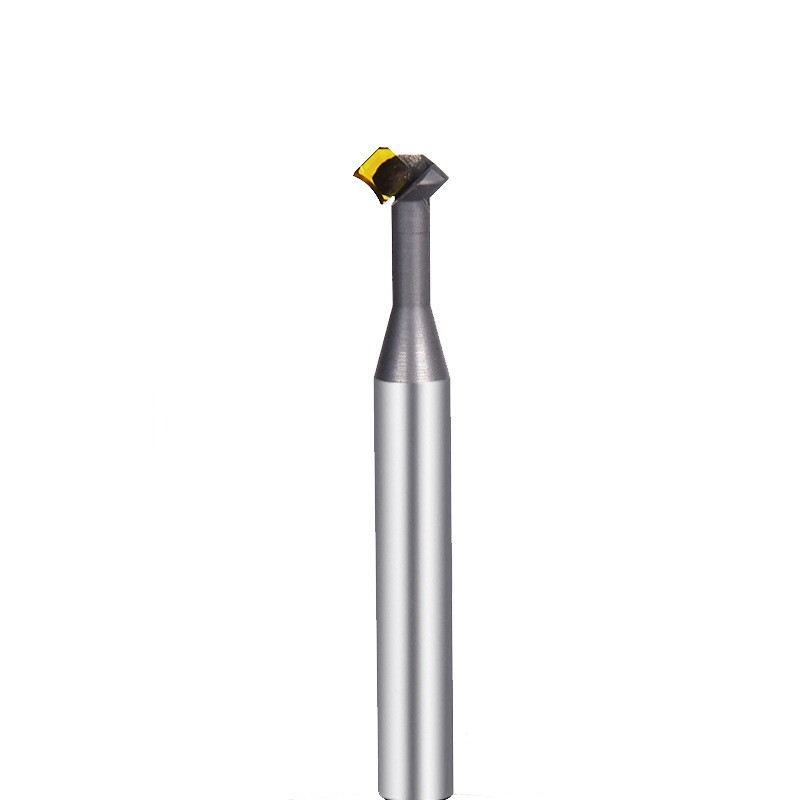
MCD Turning Tool Mirrow Finish R Cutter
Product Information Product Name Single Crystal Diamond Lower Chamfering Inner R Cutter Brand MSK Handle Material Tungsten Steel Blade Material Customized Pcd, Single Crysta […]
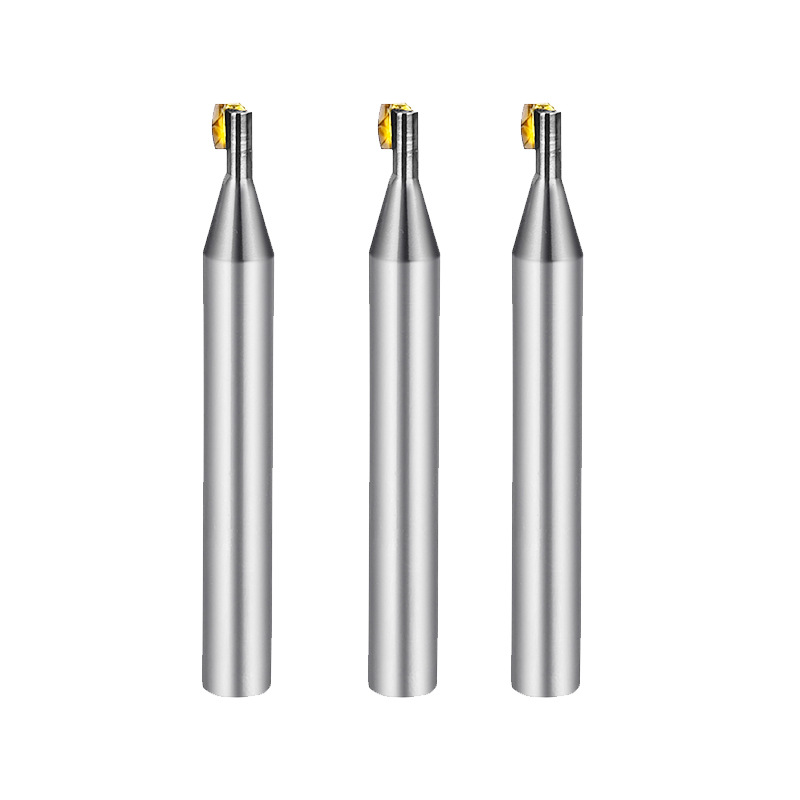
Diamond Turning Tools Outer Jewelry R Cutter
Product Information Origin Tianjing, China Material Tungsten Steel Brand Msk Type Half Round Key Milling Cutter Product Name Single Crystal Diamond Side Edge Arc Milling Cut […]
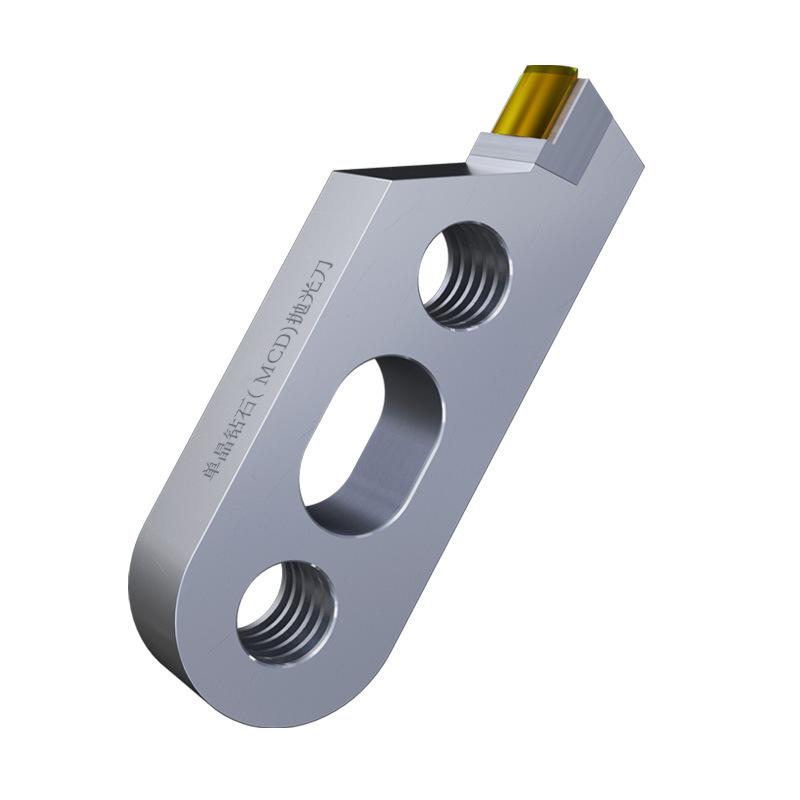
Single Crystal Diamond Polishing Cutter
Origin Tianjing, China Shank Diameter 6 (mm) Brand MSK Blade Change Method The Diamond Is Welded To The Cutter Body As A Whole Material Single Crystal Diamond (MCD) Scope Of […]
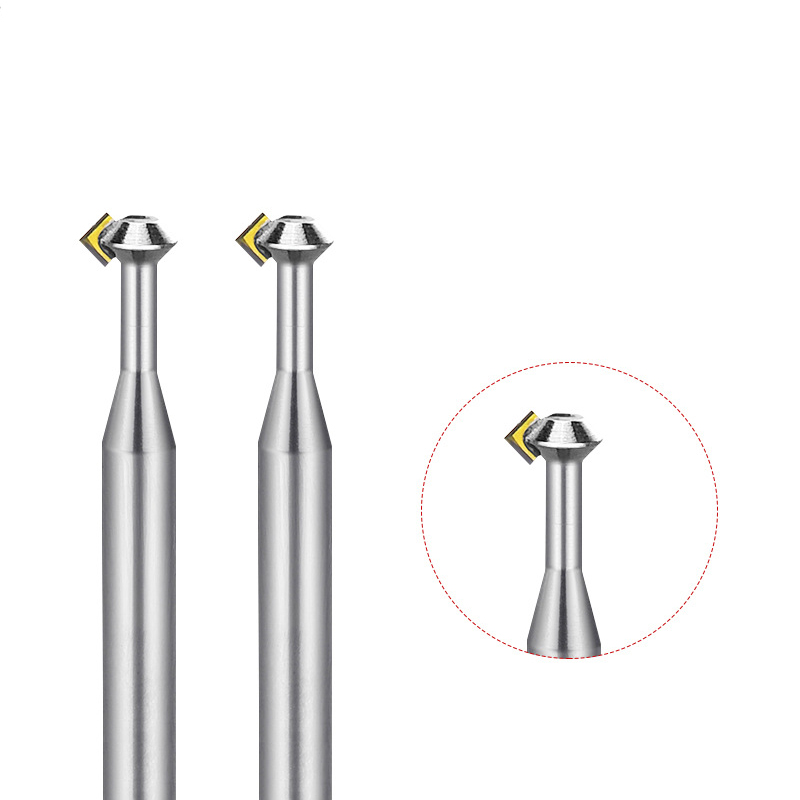
MCD High Gloss Chamfer Cutter For Gold
Product Information Origin Tianjing, China Type Flat Milling Cutter Brand Msk Whether To Coat Uncoated Series Cutter Milling Cutter Processing Range Clocks And Watches, Copp […]
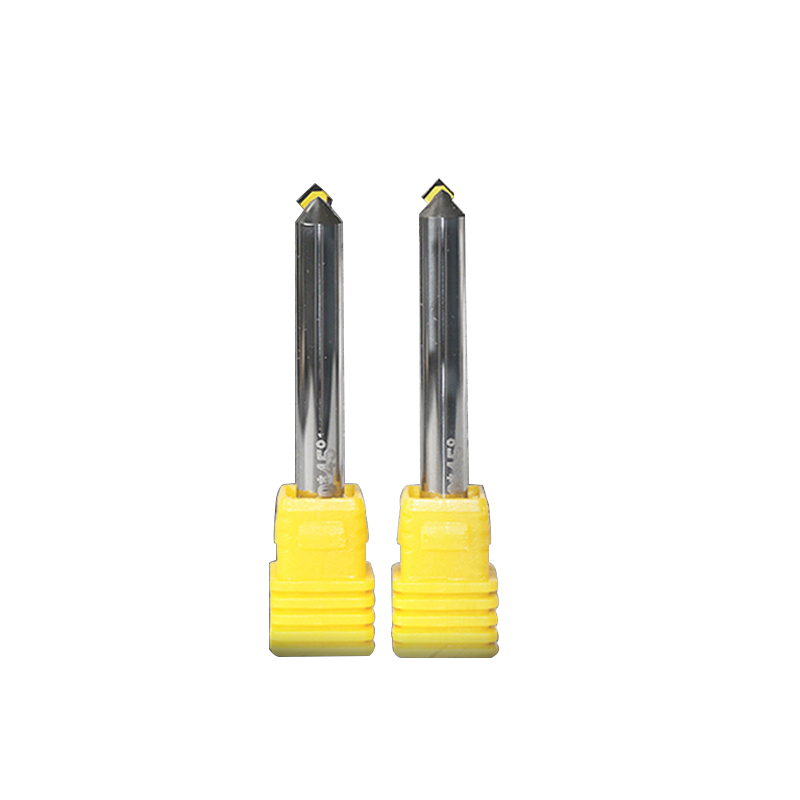
MCD Polishing Cutter for Gold Silver
Product Information Origin Tianjing, China Whether To Coat Uncoated Brand MSK Unit Weight 0.3kg Tool material Tungsten steel bar imported from Germany Product Size Shank Dia […]
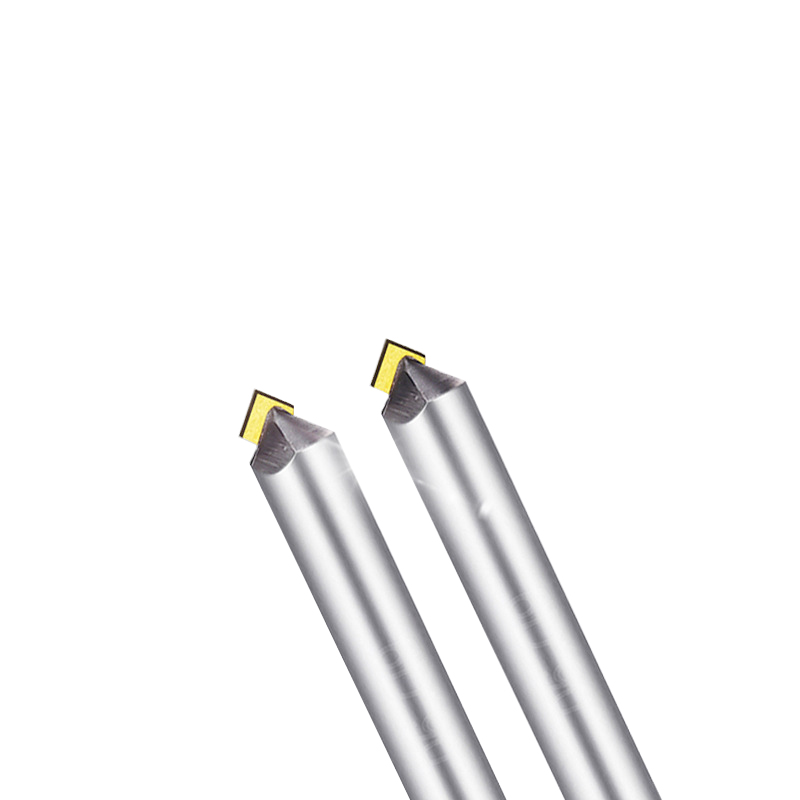
Lathe Bits MCD High Gloss Chamfer Tool
Product Information Origin Tianjing, China Cutting Edge Form Straight Edge Brand MSK Material Single Crystal Diamond Chamfer Angle 30°-180° Type Angle Milling Cutter Minimum […]
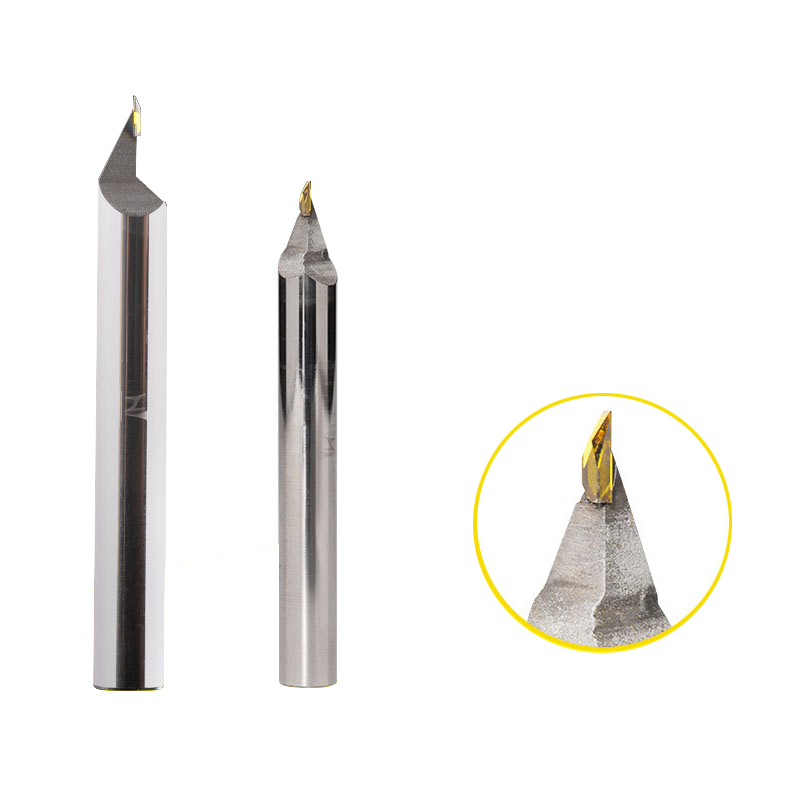
CVD/PVD/MCD Gold Jewelry Diamond Engraving Cutter
Parameter Product Name Single Crystal Diamond Carving Cutter Rotating Speed 10000-30000r/min Tool Nose Width 0.1-6.0mm Feed 1500-5000mm/min Blade Material Single Crystal Dia […]
Post time: 2023-06-30