From centuries past to the present day, the artistry of diamond cutting has been honed to a delicate, exacting degree. And now, a savvy jeweler’s cutting method of choice is wet diamond cutting, rapidly making strides in the jewelry scene and lauded for its advantages compared to more conventional diamond-shaping approaches.
In diamond cutting, wet cutting immerses the gem in a liquid concoction prior to the procedure. This fluid blend generally comprises of water plus a cleaning agent, which helps keep the diamond cool and oiled up during the cut, limiting friction created in the process. This contributes to protecting the diamond’s composition while reducing the chances of breakage or fracturing.
To begin the wet diamond cutting process, the diamond is submerged in a specific liquid solution. Subsequently, the diamond is delicately placed upon an expertly crafted diamond cutting wheel and then rotated gently to create the desired form. The ongoing cooling and lubrication of the gemstone by the liquid mixture prevents it from overheating which could lead to it fracturing or becoming damaged.
After configuring the diamond into the specified shape, it is removed from the liquid mix and allowed to air-dry. Following the drying step, a glossy, sleek finish is applied using diamond-polished wheels; this helps to maximize the stone’s radiance and mesmerizing glimmer.
Wet diamond cutting is growing in prominence within the jewelry industry as a result of its wide range of merits. The most noteworthy being the higher accuracy that this approach facilitates. The cooling and lubrication that happen during this cutting process allows a more exact final shape to be created than with regular dry diamond cutting procedures. Plus, wet diamond cutting offers lower chances of chips and fissures appearing, while uplifting the overall diamond quality.
In the domain of diamond cutting, wet cutting is becoming a more sought-after technique due to its extensive benefits. From heightened precision to lower risk of imperfections like chipping and cracking resulting from the cutting process, wet diamond cutting offers both improved accuracy and increased longevity of the diamonds involved. Ultimately, those who seek to create beautiful pieces of jewelry that can be worn for years to come are turning to wet diamond cutting with increasing frequency.
For intricate diamond cutting in jewelry making, gem crafting, and similar projects, one incredibly useful tool is the wet diamond cutter. Favored for its precision and speed, this highly specialized device can quickly shape diamonds to desired size and form with remarkable accuracy.
A wet diamond cutter boasting a blade of steel or tungsten carbide commands a diamond abrasive coating plus lubrication from a blend of oil and water. This allows the tool to tunnel through diamond material without snagging or heating up. Once attached to a handle, the cutting process begins with manual force.
Precision and delicacy are hallmarks of cutting diamonds, which require the highest quality diamond cutter to craft a vast array of shapes and sizes; including round, princess, cushion, emerald, and marquise. To ensure minimal waste of diamond material and maximum accuracy, it’s imperative that the wet diamond cutter is of the most paramount standard. The time consuming procedure needs to be conducted with precision in order to create a flawless diamond form.
Proper lubrication of the diamond is an essential practice when utilizing a wet diamond cutter to ensure the optimal efficiency of the tool. Keeping the diamond wet minimizes binding with the blade, thus avoiding an extreme rise in temperature that could potentially damage it. Additionally, lubrication serves to safeguard the diamond from wear that can be caused by the sharp-tipped blade.
To bring out its magnificent luster, the diamond is polished with a wheel of diamond abrasive affixed to a wet cutter. This process eradicates any imperfections accrued during the cutting, ultimately unveiling the stone’s exceptionally radiant allure.
To ensure a diamond’s stability in its desired setting, jewellers make use of a wet diamond cutter and a setting tool normally crafted out of gold or platinum. The tool is utilized to hold the diamond in place and guarantee that it will remain immovable and continue to sparkle magnificently without any disruption. Diamond cutting and polishing are also achieved through the use of the wet diamond cutter.
For flawless diamond cutting, polishing, and setting, the ideal tool is a top-notch wet diamond cutter. To maintain its high-quality performance, proper care must be taken to ensure that it is kept in pristine condition for as many years as possible. With a reliable wet diamond cutter in hand, you can guarantee beautiful results for your diamonds every time.
Related Product
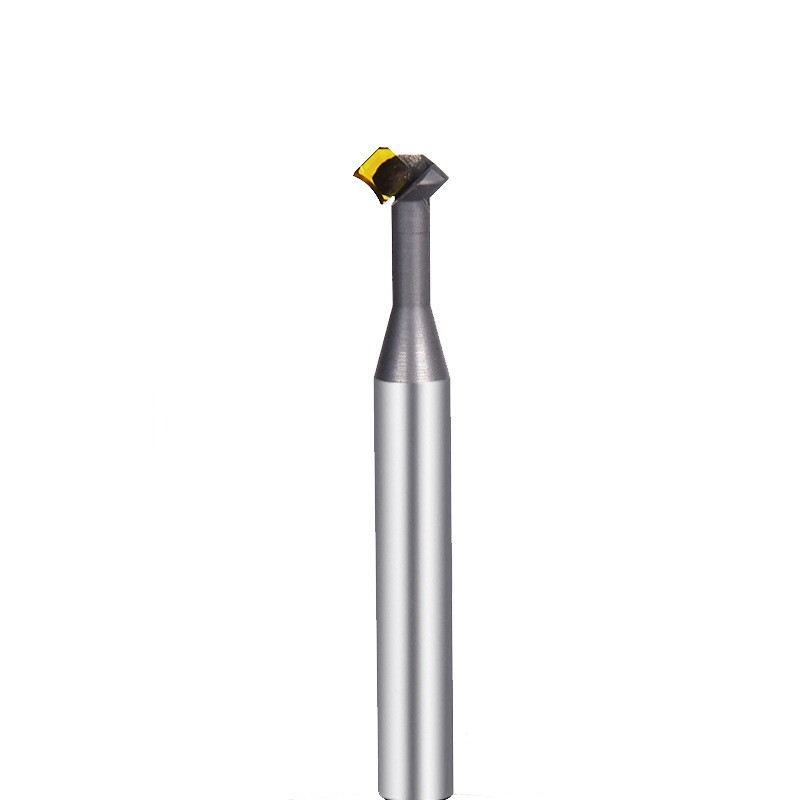
MCD Turning Tool Mirrow Finish R Cutter
Product Information Product Name Single Crystal Diamond Lower Chamfering Inner R Cutter Brand MSK Handle Material Tungsten Steel Blade Material Customized Pcd, Single Crysta […]
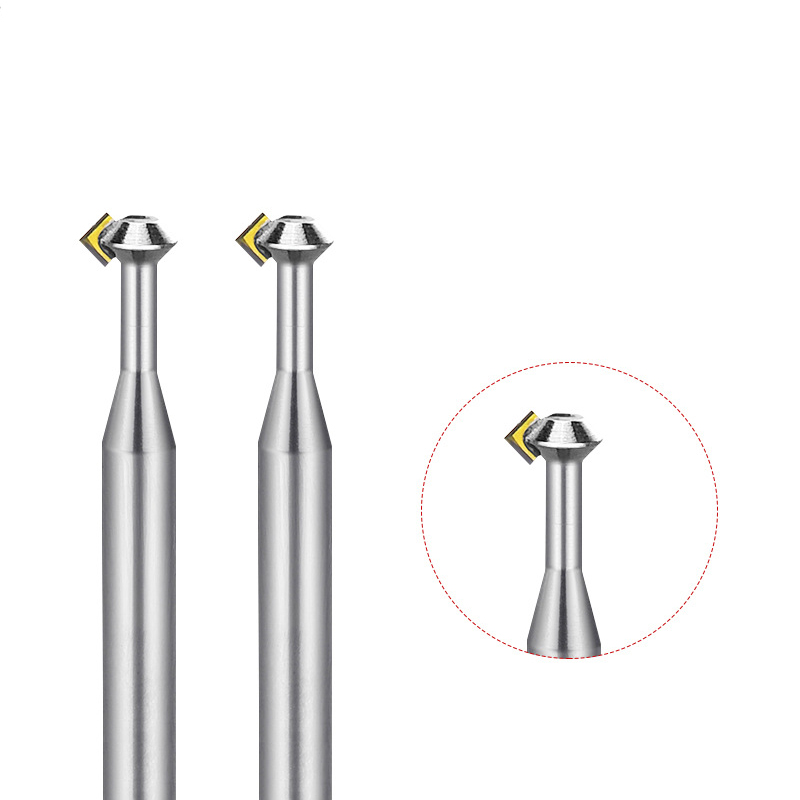
MCD High Gloss Chamfer Cutter For Gold
Product Information Origin Tianjing, China Type Flat Milling Cutter Brand Msk Whether To Coat Uncoated Series Cutter Milling Cutter Processing Range Clocks And Watches, Copp […]
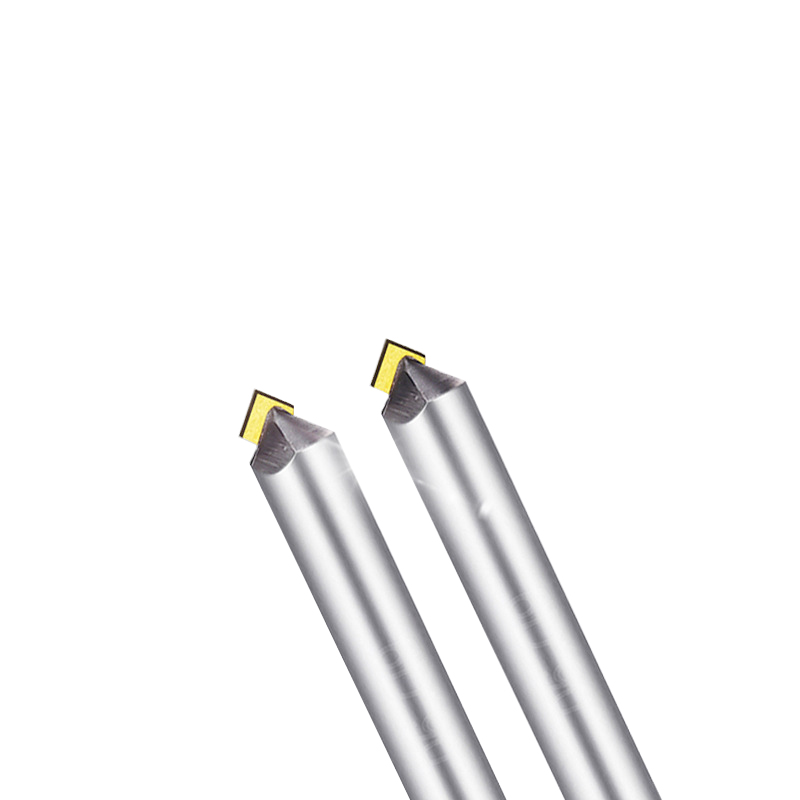
Lathe Bits MCD High Gloss Chamfer Tool
Product Information Origin Tianjing, China Cutting Edge Form Straight Edge Brand MSK Material Single Crystal Diamond Chamfer Angle 30°-180° Type Angle Milling Cutter Minimum […]
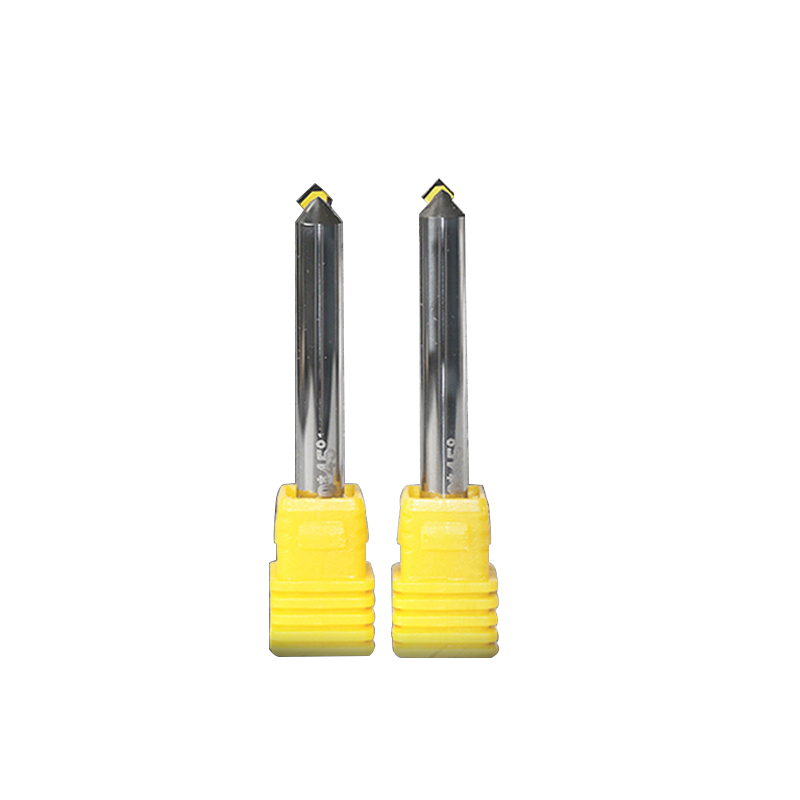
MCD Polishing Cutter for Gold Silver
Product Information Origin Tianjing, China Whether To Coat Uncoated Brand MSK Unit Weight 0.3kg Tool material Tungsten steel bar imported from Germany Product Size Shank Dia […]
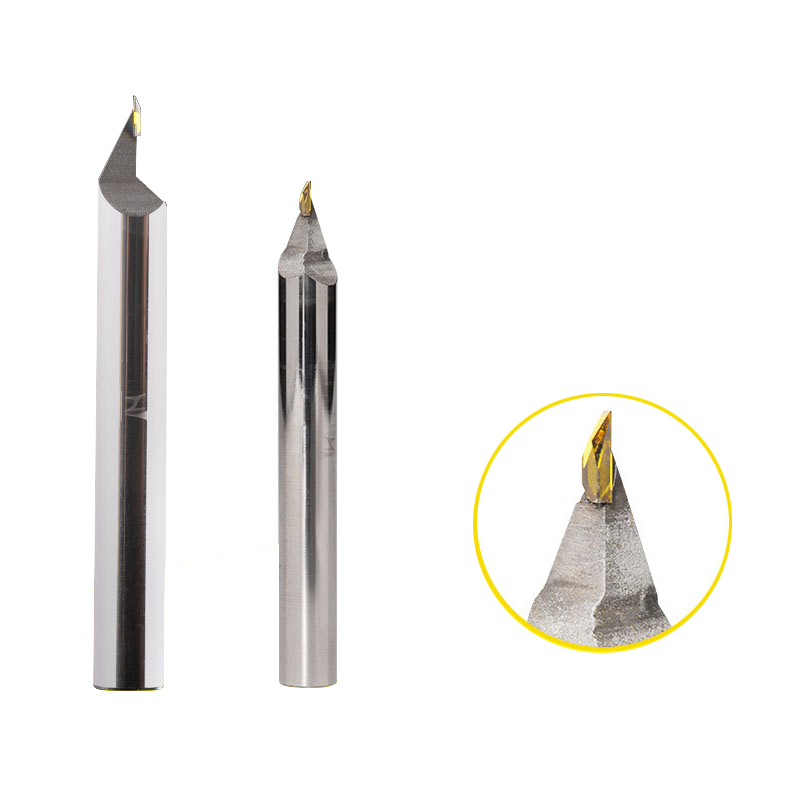
CVD/PVD/MCD Gold Jewelry Diamond Engraving Cutter
Parameter Product Name Single Crystal Diamond Carving Cutter Rotating Speed 10000-30000r/min Tool Nose Width 0.1-6.0mm Feed 1500-5000mm/min Blade Material Single Crystal Dia […]
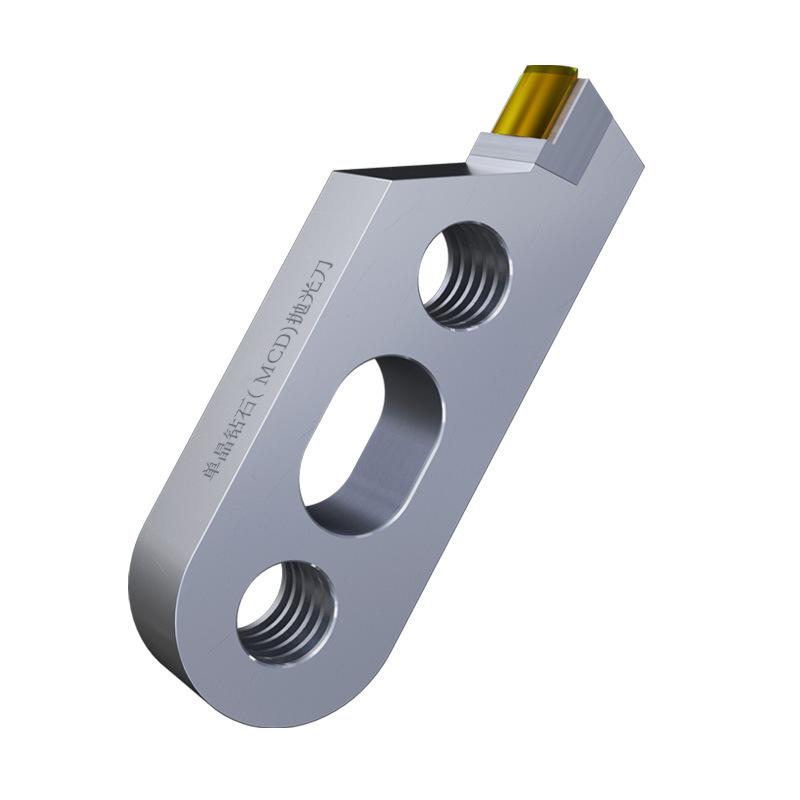
Single Crystal Diamond Polishing Cutter
Origin Tianjing, China Shank Diameter 6 (mm) Brand MSK Blade Change Method The Diamond Is Welded To The Cutter Body As A Whole Material Single Crystal Diamond (MCD) Scope Of […]
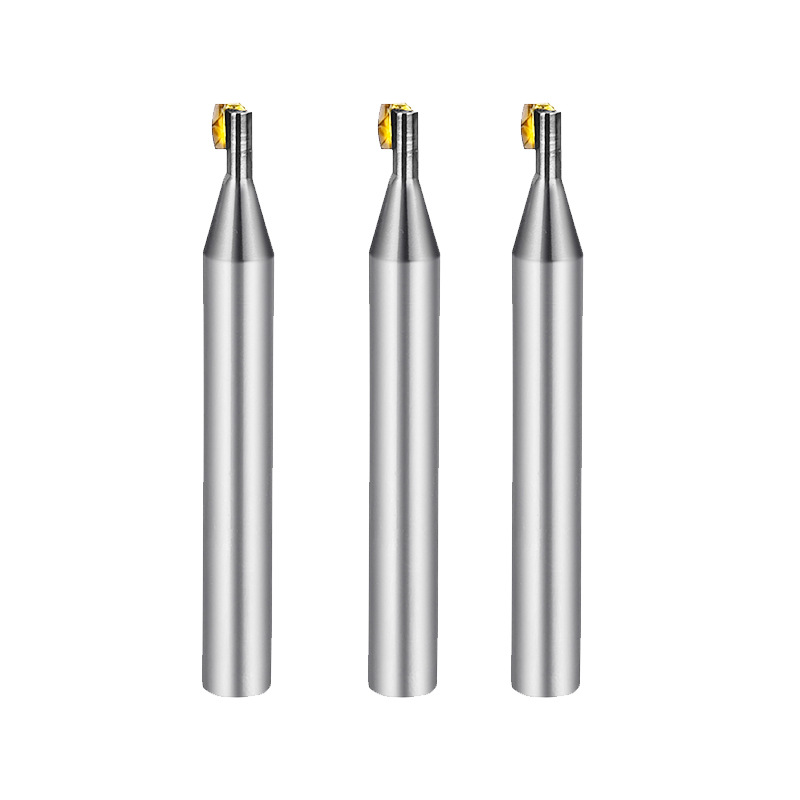
Diamond Turning Tools Outer Jewelry R Cutter
Product Information Origin Tianjing, China Material Tungsten Steel Brand Msk Type Half Round Key Milling Cutter Product Name Single Crystal Diamond Side Edge Arc Milling Cut […]
Post time: 2023-08-10