For optimal performance and longevity when working with hard materials like rocks and concrete, mining and drilling operations rely heavily on the use of polycrystalline diamond cutter bits. Crafted from a blend of diamond and metal abrasive particles, PCD bits are renown for their even wear and tear that outlast traditional cutting tools. Not only do they speed up the process of slicing through rugged surfaces, but they are also more dependable in the long run.
Polycrystalline diamond cutter bits are best known for their superior strength and extreme resistance to wear. Their impressive durability makes them an easy choice when it comes to drilling and mining operations that require reliable cutting tools. On top of being able to withstand even the toughest materials, these bits make quick work of them, quickly and cleanly cutting through whatever they come into contact with. Such high efficiency makes these cutting bits a cost-effective solution for any mining or drilling project that needs materials to be cut through promptly.
Polycrystalline diamond cutter bits bring a host of benefits to the table. Not only are they capable of withstanding the rigors of high-temperature environments, but they boast a strong resistance to corrosion and any external damage that could otherwise compromise their performance. On top of this, the particles used in their fabrication are available at prices that make them an attractive and cost-effective solution for a variety of mining and drilling applications.
Crafted from a combination of tough diamond and metal abrasive particles, polycrystalline diamond bits are ideal for heavy-duty drilling and mining operations. These robust cutters offer a superior approach to slicing through difficult materials, including rocks, concrete, and more. An efficient cutting action with the durability to last, these bits are essential for tackling tedious tasks with ease.
Polycrystalline diamond cutter bits can prove useful in a bevvy of activities. From expeditiously chipping away at minerals and ore in the mining and drilling sector, to breaking through the toughest of concrete in construction projects, these cutter bits are go-to when hard materials stand in the way. What’s more, they are regularly employed for precision cutting in the manufacturing trade for metals and the like.
Polycrystalline diamond cutter bits are characterized by their ease of use and maintenance. These tools require minimal upkeep and can be put into action multiple times before needing to be renewed. To keep the bits in ideal circumstances, regular cleaning and sharpening is recommended. Furthermore, to preserve these cutting tools and make sure they remain secure from outside harm, store them in a cool, dry place.
When it comes to reliable and economical operations, polycrystalline diamond cutter bits top the list. Their tremendous strength and durability makes them an ideal option for cutting through tough materials, while their resistance to heat and corrosion make them suitable for use around high temperatures. Plus, the abrasive particles used in their production boast a pretty low price tag, granting a cost-effective solution for any need.
Diamonds have held an integral role in industrial applications for centuries due to their remarkable hardness. As the need for improved diamond cutting techniques emerged, so did the development of more advanced tools. One of the latest innovations is polycrystalline diamond cutter bits, combining synthetic and natural diamond particles for uncomparable results. By using this cutting-edge technology, remarkable gains can be made in efficiency, lifespan, and the quality of the end product.
For tough materials, such as metals and ceramics, the single crystal diamond cutter bit is the way to go. These bits are typically constructed from a solitary diamond crystal, giving them the strength and accuracy needed for even the most intense cutting situations. Of course, such power comes with a cost– these cutters can be quite expensive, and need replacing more often than most.
The bonds between synthetic and natural diamond particles are sealed by a unique adhesive, resulting in the exceptional strength of a polycrystalline diamond cutter bit. This strength grants the bit durability that surpasses that of the traditional diamond cutting tool, dominating more projects with fewer replacements necessary. Laborers are guaranteed a longer expanse of time before inkling to switch out bits.
A polycrystalline diamond cutting bit possesses numerous benefits compared to traditional diamond cutting tools. For example, the way in which it binds the diamond particles together reduces the friction between the bit and the material it is slicing. Therefore, this helps to prevent extreme heat buildup which can harm both the cutting substance as well as the bit itself. Furthermore, its diamond particles are strongly resistant to chipping and breaking, granting the bit extended sturdiness as opposed to a single crystal bit.
Exponentially increased surface area affords polycrystalline diamond cutter bits a significant advantage over single crystal bits – they are considerably more efficient. The multiple diamond particles bonded together create a multiplied cutting surface, allowing for operations to take place faster and profit from an enhanced level of accuracy. Furthermore, the amplified power of this design permits the bit to penetrate a variety of otherwise impenetrable materials.
Industrial diamond cutting applications are increasingly turning to polycrystalline diamond cutter bits as a way to enhance productivity and maximize tool endurance. This is because the increased hardness and surface area of the bit permit it to complete cuts with heightened precision and velocity, while also being more resilient than a single crystal bit. Furthermore, the reduced friction and temperate buildup during operation lead to sleeker incisions while minimizing harm to the material being cut. Consequently, polycrystalline diamond cutter bits are quickly becoming a favorite in this field.
Related Product
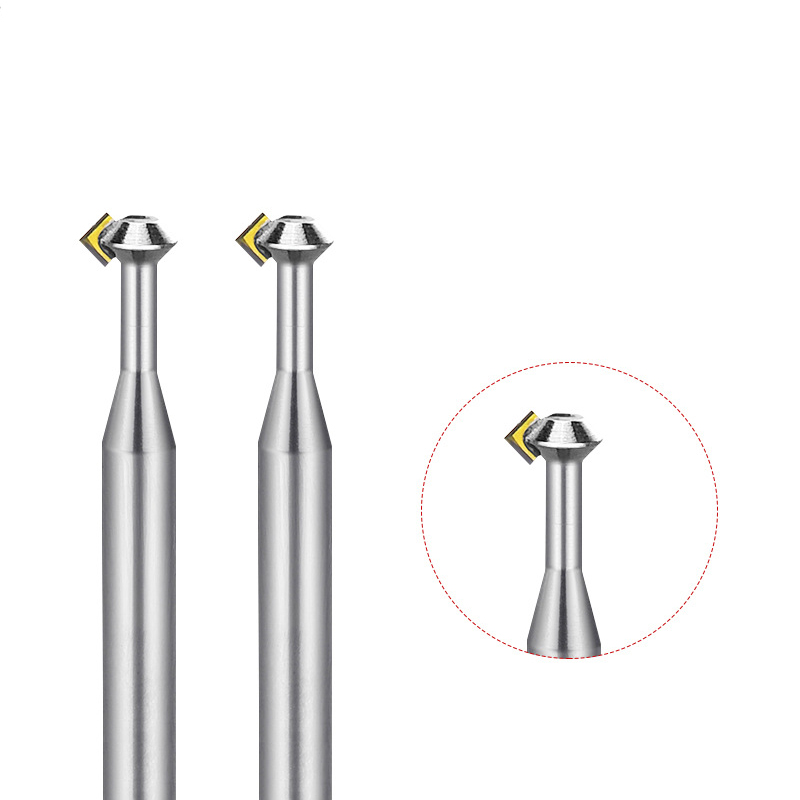
MCD High Gloss Chamfer Cutter For Gold
Product Information Origin Tianjing, China Type Flat Milling Cutter Brand Msk Whether To Coat Uncoated Series Cutter Milling Cutter Processing Range Clocks And Watches, Copp […]
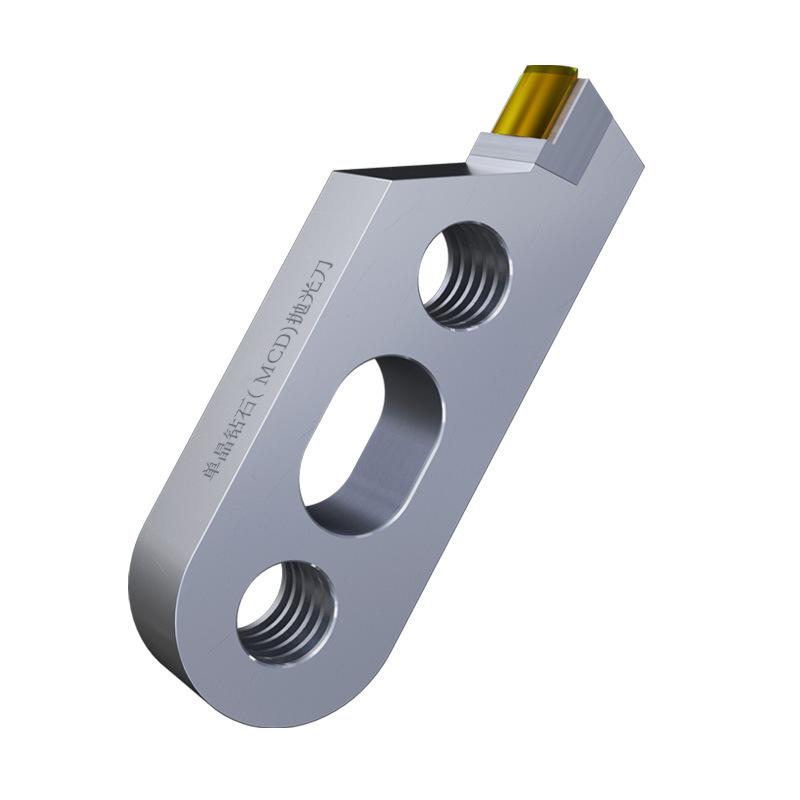
Single Crystal Diamond Polishing Cutter
Origin Tianjing, China Shank Diameter 6 (mm) Brand MSK Blade Change Method The Diamond Is Welded To The Cutter Body As A Whole Material Single Crystal Diamond (MCD) Scope Of […]
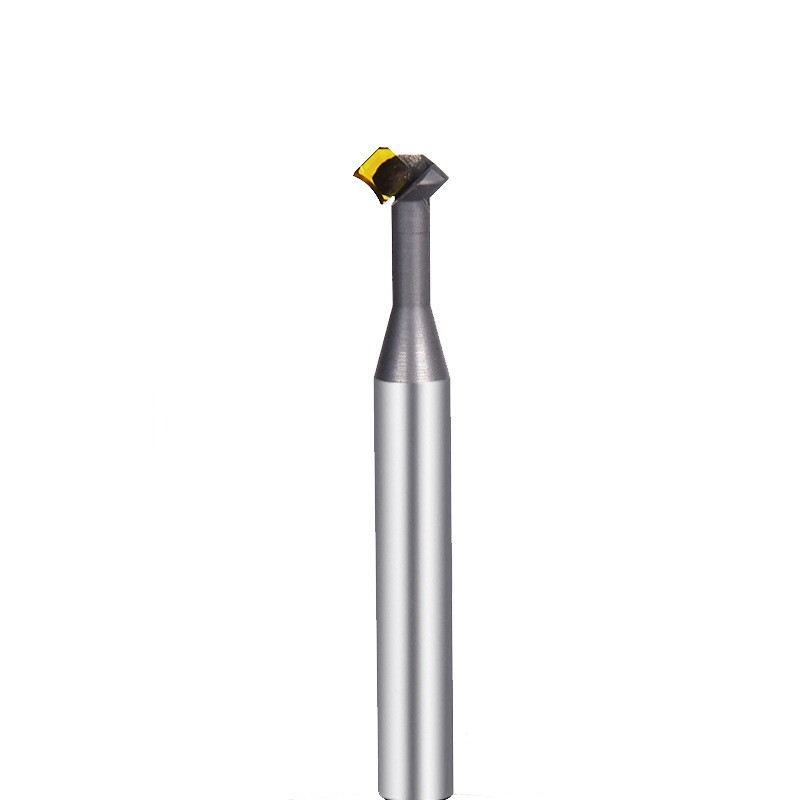
MCD Turning Tool Mirrow Finish R Cutter
Product Information Product Name Single Crystal Diamond Lower Chamfering Inner R Cutter Brand MSK Handle Material Tungsten Steel Blade Material Customized Pcd, Single Crysta […]
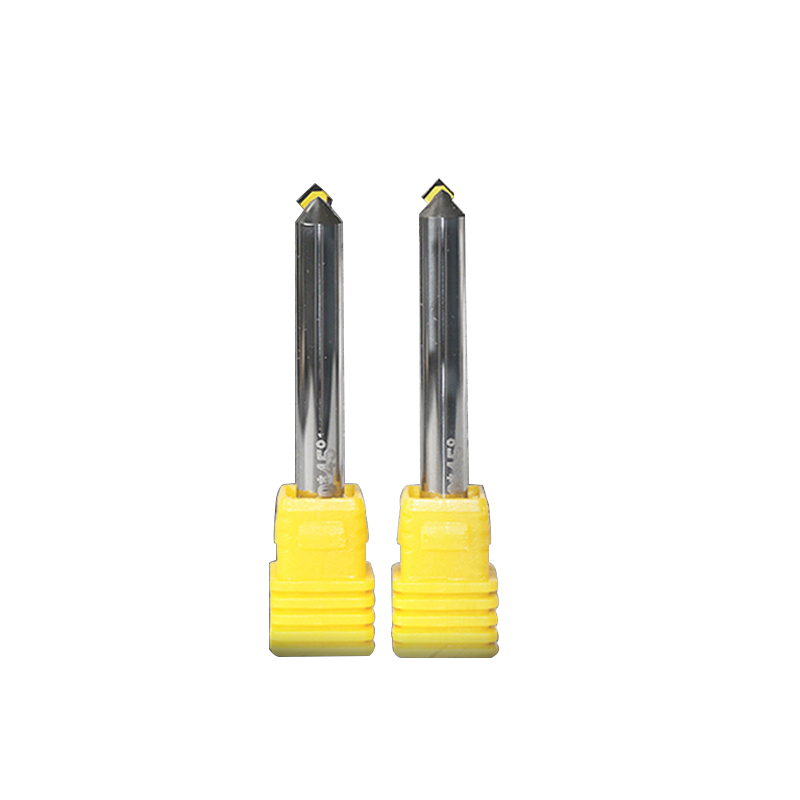
MCD Polishing Cutter for Gold Silver
Product Information Origin Tianjing, China Whether To Coat Uncoated Brand MSK Unit Weight 0.3kg Tool material Tungsten steel bar imported from Germany Product Size Shank Dia […]
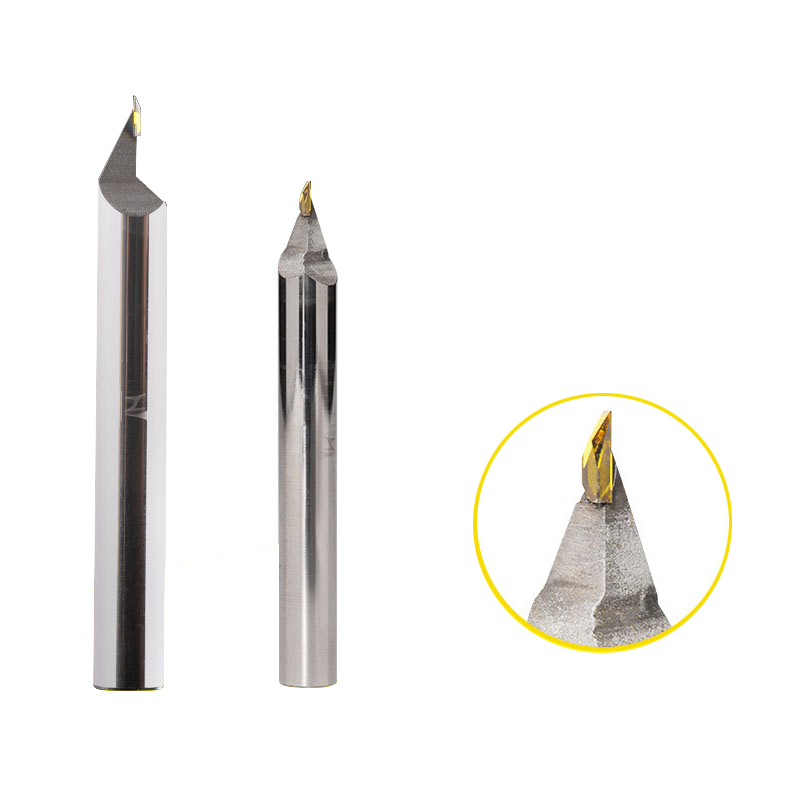
CVD/PVD/MCD Gold Jewelry Diamond Engraving Cutter
Parameter Product Name Single Crystal Diamond Carving Cutter Rotating Speed 10000-30000r/min Tool Nose Width 0.1-6.0mm Feed 1500-5000mm/min Blade Material Single Crystal Dia […]
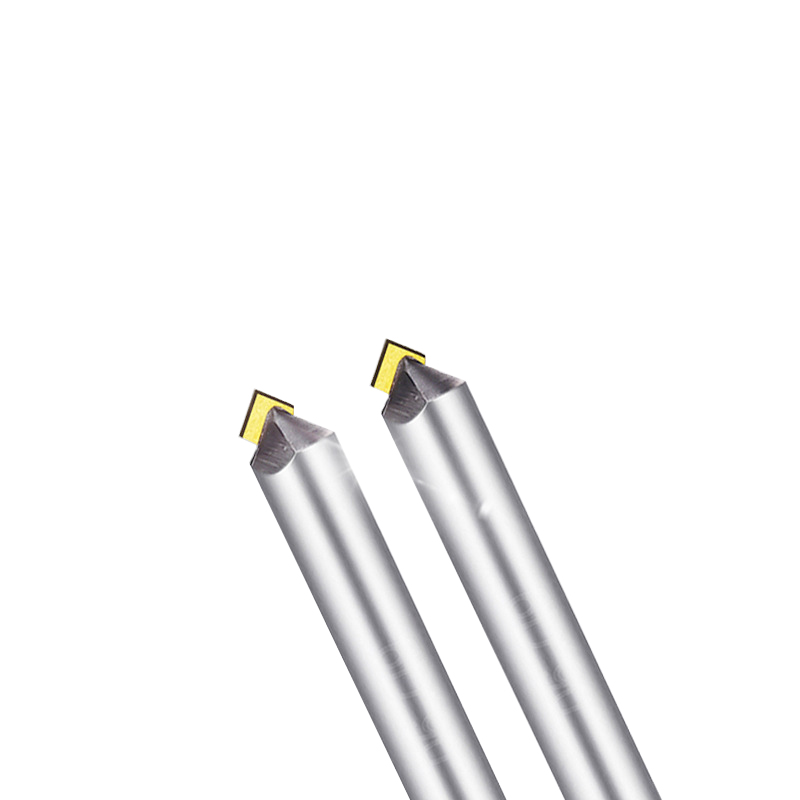
Lathe Bits MCD High Gloss Chamfer Tool
Product Information Origin Tianjing, China Cutting Edge Form Straight Edge Brand MSK Material Single Crystal Diamond Chamfer Angle 30°-180° Type Angle Milling Cutter Minimum […]
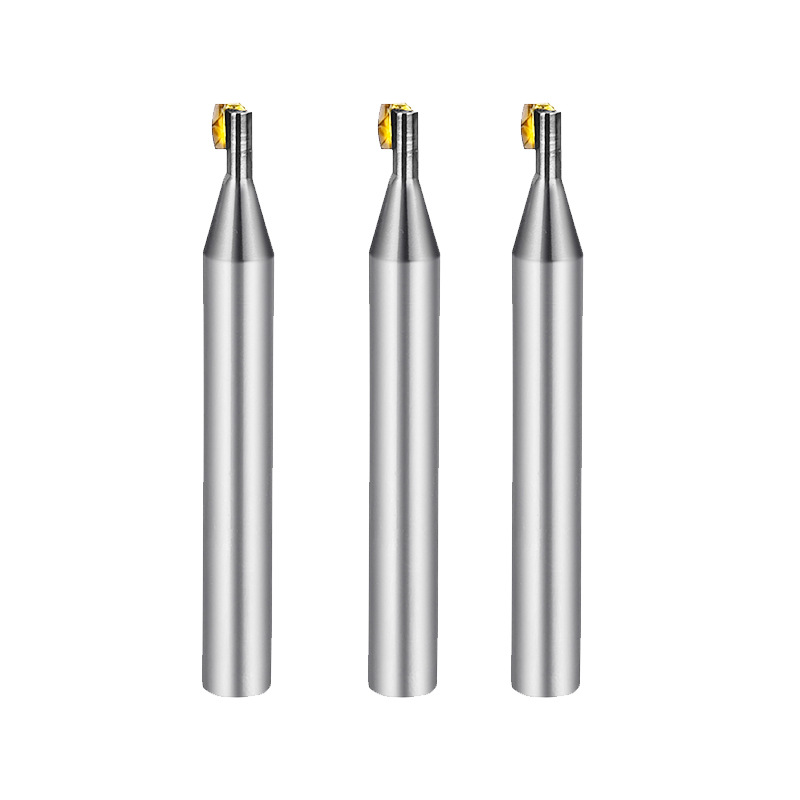
Diamond Turning Tools Outer Jewelry R Cutter
Product Information Origin Tianjing, China Material Tungsten Steel Brand Msk Type Half Round Key Milling Cutter Product Name Single Crystal Diamond Side Edge Arc Milling Cut […]
Post time: 2023-08-09