Essential to machining, PCD (polycrystalline diamond) cutters are much sought after due to their superior quality and longevity. Whether they are suitable for your operations ultimately comes down to an assessment of both the advantages and disadvantages of using this type of milling cutter.
Unlocking the Advantages of PCD Milling Cutters
PCD milling cutters are renowned for their amazingly long lifespans, due to being simply indestructible. A PCD cutter is created through the fusion of diamond particles and a metal matrix, leaving it almost impossible to degrade. This makes it the perfect tool for machining tasks that require consistency and accuracy for sustained periods of time. Moreover, their powerful composition allows them to excel in slicing through dubious-to-cut materials like aluminum, graphite, plastics, and composites.
PCD milling cutters boast immense user-friendliness and a remarkably low maintenance requirement. Furthermore, they boast an impressive cutting edge length that gives a pleasing finish with little or no further polishing required, plus unparalleled cutting speed, so they are impeccable for industrial-scale production runs.
PCD milling cutters are not only advantageous in terms of performance but also in terms of value. Compared to regular cutting tools, you will find that the price is quite reasonable. Furthermore, the impressive longevity of PCD cutters means that you will only need to purchase replacements infrequently, compounding their cost-effectiveness and making your initial outlay more economical in the long run.
Adverse Effects of PCD Milling Cutters
While PCD milling cutters boast numerous advantages, they are not suitable for all materials. In particular, when it comes to materials like steel or stainless steel, they may not be the most effective option. On the other hand, they do work best with softer materials such as aluminum and plastics.
Rather than being as malleable as regular cutting tools, PCD milling cutters are intended for use in particular circumstances and could be unsuitable for complicated machining jobs. As a result, it is wise to exercise caution and take the time to plan properly before utilizing them.
In conclusion, PCD cutters are not a universal solution. Their demanding precision specifications limit their compatibility with older machining systems. Additionally, the coolant required to keep these tools from heat-damage limits their use with some types of machinery.
PCD milling cutters offer countless benefits over classic cutting tools, such as greater resilience, effortless operation, and affordability. Nevertheless, they may not be suitable for all machine types and materials; thus, requiring proper research and concern prior to utilization. Ultimately, the option to use PCD milling cutters is rooted in the individual demands of the machining process.
Exploring the Benefits and Potential Drawbacks of PCD Milling Cutters
For materials such as aluminum, titanium, and some steel, PCD (polycrystalline diamond) milling cutters are the specialised cutting tool that can get the job done. Unlike traditional cutting tools, these milling cutters are designed with a diamond tip securely fused to a tungsten carbide backing. This ingenious synthesis of materials gives them incomparable strength and an impressive capacity to drill into the toughest circumstances.
If you’re looking for a milling cutter that offers top-notch benefits, considering a model with a Polycrystalline Diamond tool might be the right move. Still, it’s important to recognize there are also some drawbacks associated with this type of milling cutter, so make sure you understand all of the pros and cons before making your decision.
The longevity of PCD milling cutters is unparalleled, making them the perfect choice for cutting applications requiring sharp, consistent precision. With proper care, they can last for years, thanks to a diamond tip designed for extended sharpness and a tungsten carbide substrate that prevents potential brittleness.
PCD milling cutters are versatile tools, perfect for projects that involve cutting through diverse materials; aluminum, titanium, and certain steel alloys are capable of being processed. This gives these milling cutters an edge over competitors in terms of the sheer variety of materials they can work with.
PCD milling cutters are fantastic options for projects that involve speed, such as production lines and other high-pressure cut-rate applications. These cutting tools provide better speeds than traditional materials, making them a premier selection for time-sensitive assignments.
For certain applications, the expenses associated with PCD milling cutters may be outside of reach, making them an unaffordable option in comparison to regular cutting tools.
To maintain the PCD milling cutters to ensure they stay in great shape, regularly sharpening the diamond tip and changing out the tungsten carbide substrate is a must.
It is imperative to exercise caution with PCD milling cutters, as their diamond tips may chip and break if treated carelessly. Such a mishap can get expensive, resulting in the need for repairs or even a full replacement.
When it comes to machining, PCD milling cutters are the gold standard, boasting an array of advantages such as sturdiness, inclusiveness, and nimbleness. However, it is important to keep in mind that they are typically more costly than traditional cutting tools and demand regular upkeep. Establishing a thorough understanding of the benefits and drawbacks of PCD milling cutters can help you make an informed decision about what is the best choice for your project.
Related Product
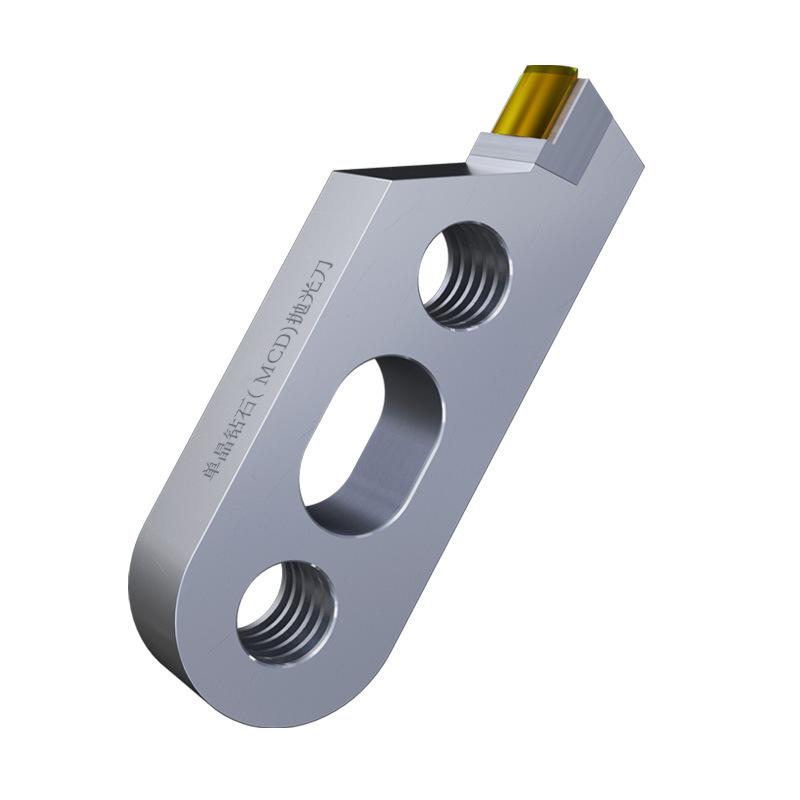
Single Crystal Diamond Polishing Cutter
Origin Tianjing, China Shank Diameter 6 (mm) Brand MSK Blade Change Method The Diamond Is Welded To The Cutter Body As A Whole Material Single Crystal Diamond (MCD) Scope Of […]
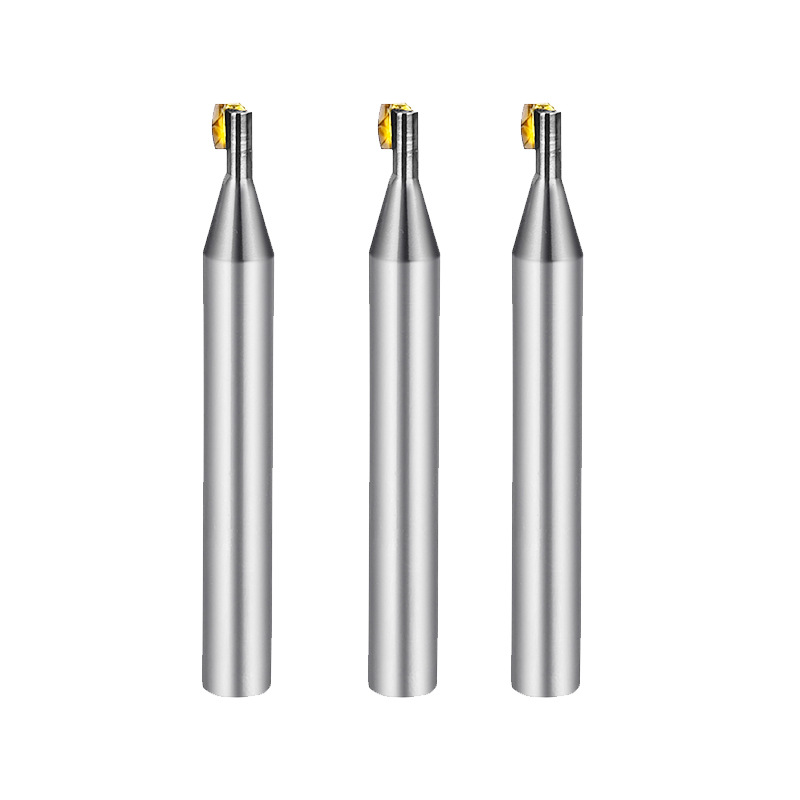
Diamond Turning Tools Outer Jewelry R Cutter
Product Information Origin Tianjing, China Material Tungsten Steel Brand Msk Type Half Round Key Milling Cutter Product Name Single Crystal Diamond Side Edge Arc Milling Cut […]
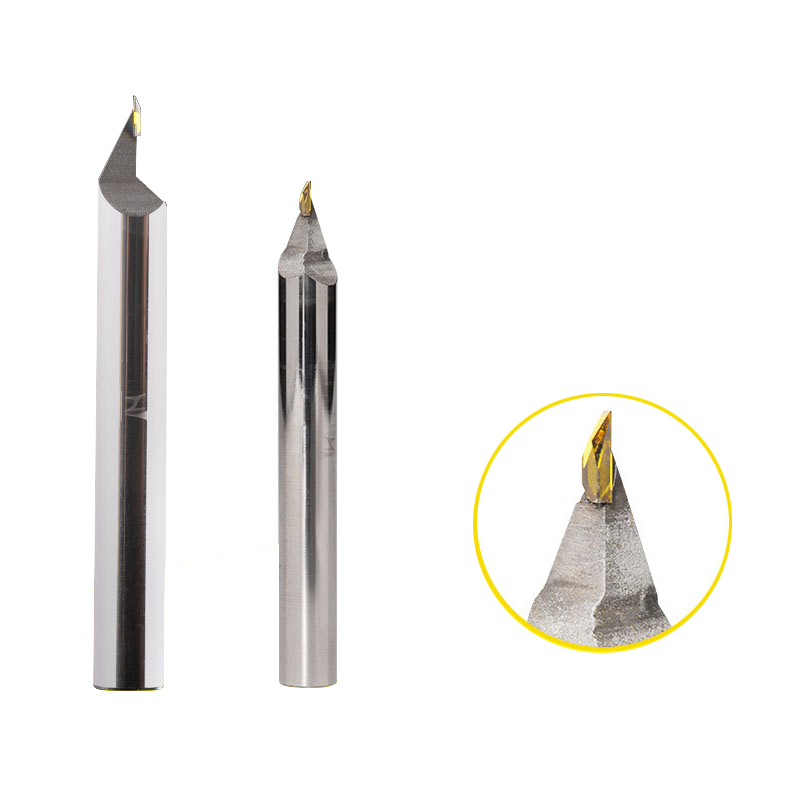
CVD/PVD/MCD Gold Jewelry Diamond Engraving Cutter
Parameter Product Name Single Crystal Diamond Carving Cutter Rotating Speed 10000-30000r/min Tool Nose Width 0.1-6.0mm Feed 1500-5000mm/min Blade Material Single Crystal Dia […]
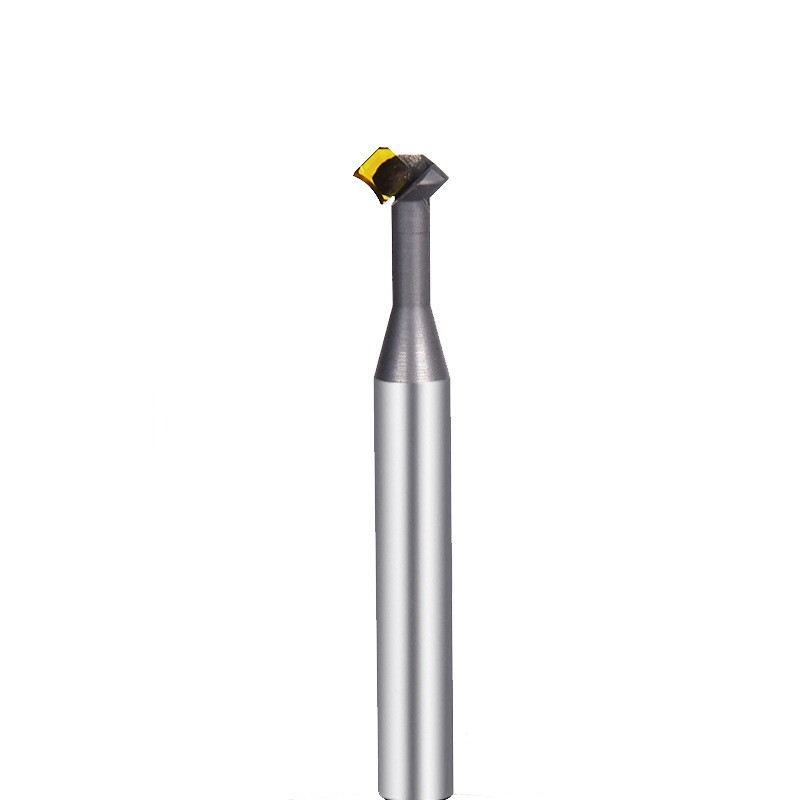
MCD Turning Tool Mirrow Finish R Cutter
Product Information Product Name Single Crystal Diamond Lower Chamfering Inner R Cutter Brand MSK Handle Material Tungsten Steel Blade Material Customized Pcd, Single Crysta […]
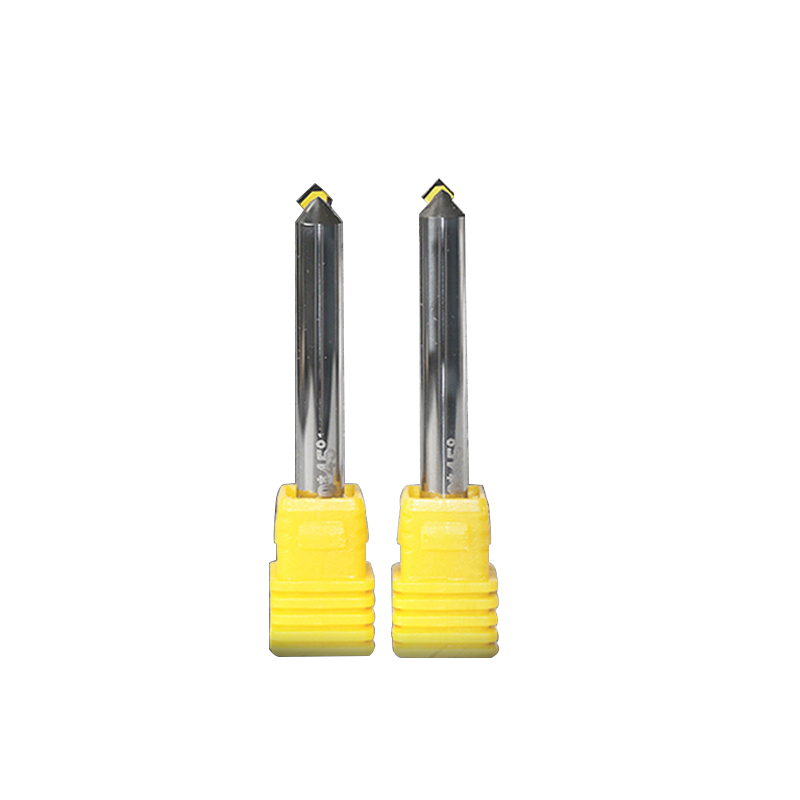
MCD Polishing Cutter for Gold Silver
Product Information Origin Tianjing, China Whether To Coat Uncoated Brand MSK Unit Weight 0.3kg Tool material Tungsten steel bar imported from Germany Product Size Shank Dia […]
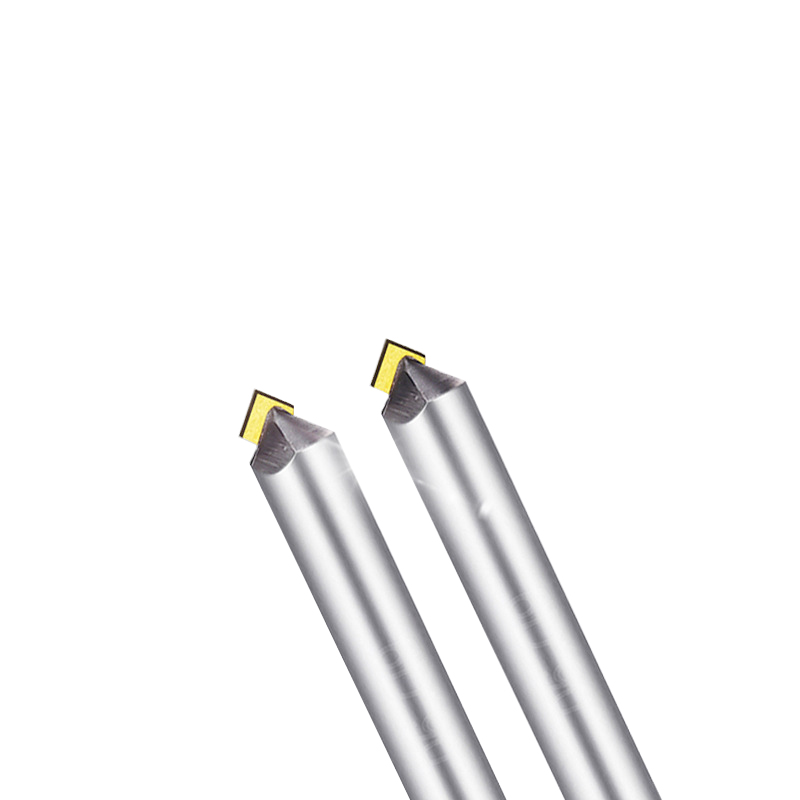
Lathe Bits MCD High Gloss Chamfer Tool
Product Information Origin Tianjing, China Cutting Edge Form Straight Edge Brand MSK Material Single Crystal Diamond Chamfer Angle 30°-180° Type Angle Milling Cutter Minimum […]
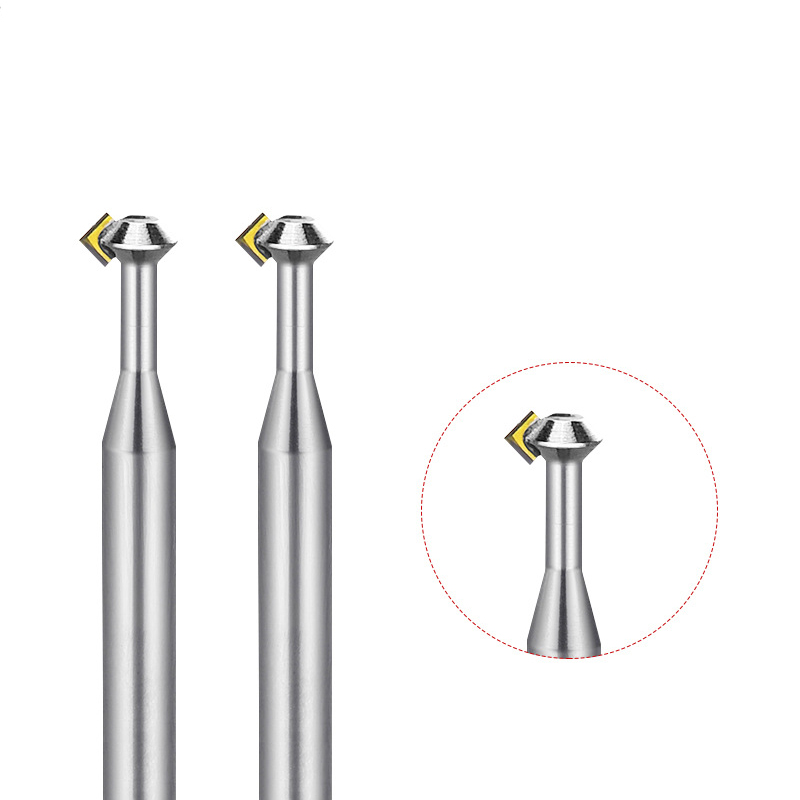
MCD High Gloss Chamfer Cutter For Gold
Product Information Origin Tianjing, China Type Flat Milling Cutter Brand Msk Whether To Coat Uncoated Series Cutter Milling Cutter Processing Range Clocks And Watches, Copp […]
Post time: 2023-07-14