Polycrystalline diamond forms the basis of a PCD insert, a cutting tool renowned for its potential to work with multiple machining processes – from turning, drilling and milling to reaming. Its durability and resistance to wear and tear make it ideal for machining materials that resist regular tools.
PCD inserts are the perfect companion for number of machining operations, like turning and milling, as the sintering-process of tiny diamond particles produces material that is extremely hard with a remarkable thermal conductivity. This combination makes these inserts capable of tackling even the most high-heat operations with ease.
PCD inserts are renowned for their reliable and robust durability when it comes to wear and tear. This is because the diamond particles, intricately connected with one another, prevent their dislodgment during machining processes that require a high degree of endurance, such as drilling and reaming.
A plethora of shapes and sizes are obtainable when it comes to getting PCD inserts, with the most prevailing being square, rectangular, and round. The size of the insert is normally in accordance with the size of the cutting tool that it will be employed in.
When it comes to machining operations, tungsten carbide is often the material of choice for PCD inserts due to its high melting point, strength, and robustness. Its advantageous properties make it capable of enduring the extreme temperatures that such processes give rise to.
To ensure durability and efficacy, PCD inserts are often adorned with a thin film of diamond covering. The most conventional approaches to this protective layering are CVD (chemical vapor deposition) and PVD (physical vapor deposition). This shielding helps maintain quality in cutting performance while defending the insert from wear.
A vast array of machining tasks can be completed utilizing PCD inserts, the most standard being turning, milling, drilling, and reaming. However, they also prove useful in more intricate projects like grinding and sawing.
When it comes to PCD inserts, tungsten carbide is often the material of choice. This is because it is substantially robust, and capable of enduring even the most exceptional of temperatures created during production processes. Its exceedingly high melting point means that one can rely on its dependable performance through extensive treatments.
To reinforce its cutting performance and safeguard it from wear, a PCD insert is regularly clad with a protective layer of diamond. Most often, this is executed through either CVD or PVD, both chemical and physical vapor deposition techniques.
A broad array of machining tasks make use of PCD inserts. These components are commonly used in turning, drilling, milling, and reaming, but can also be employed in operations such as sawing or grinding.
Related Product
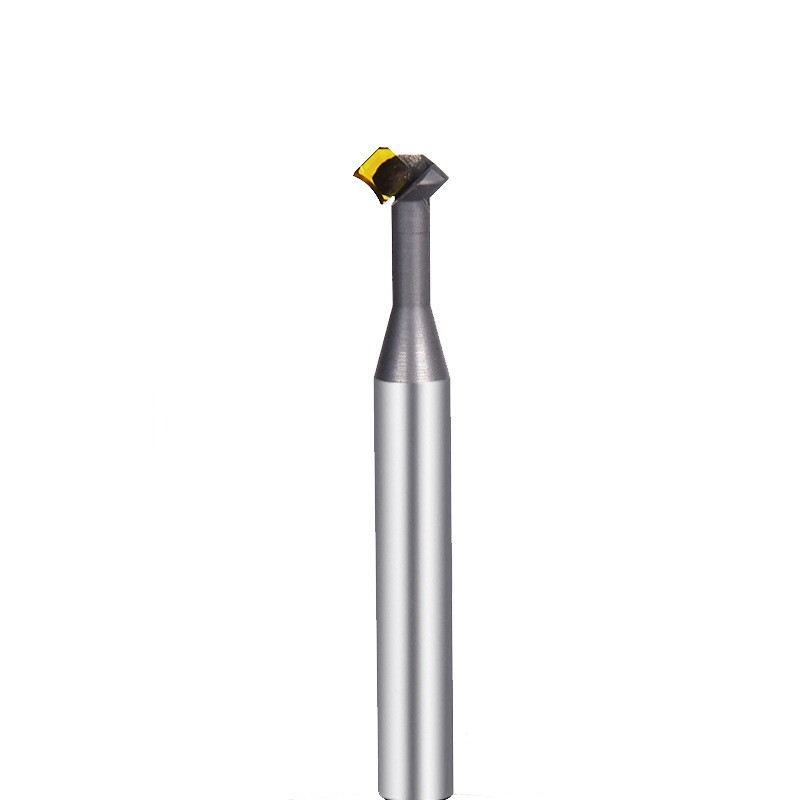
MCD Turning Tool Mirrow Finish R Cutter
Product Information Product Name Single Crystal Diamond Lower Chamfering Inner R Cutter Brand MSK Handle Material Tungsten Steel Blade Material Customized Pcd, Single Crysta […]
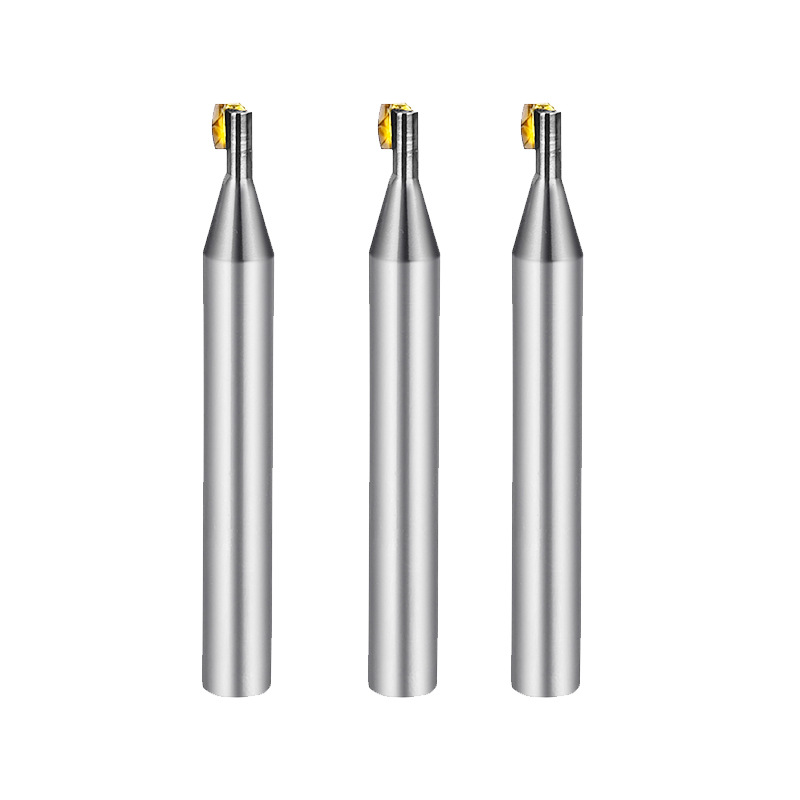
Diamond Turning Tools Outer Jewelry R Cutter
Product Information Origin Tianjing, China Material Tungsten Steel Brand Msk Type Half Round Key Milling Cutter Product Name Single Crystal Diamond Side Edge Arc Milling Cut […]
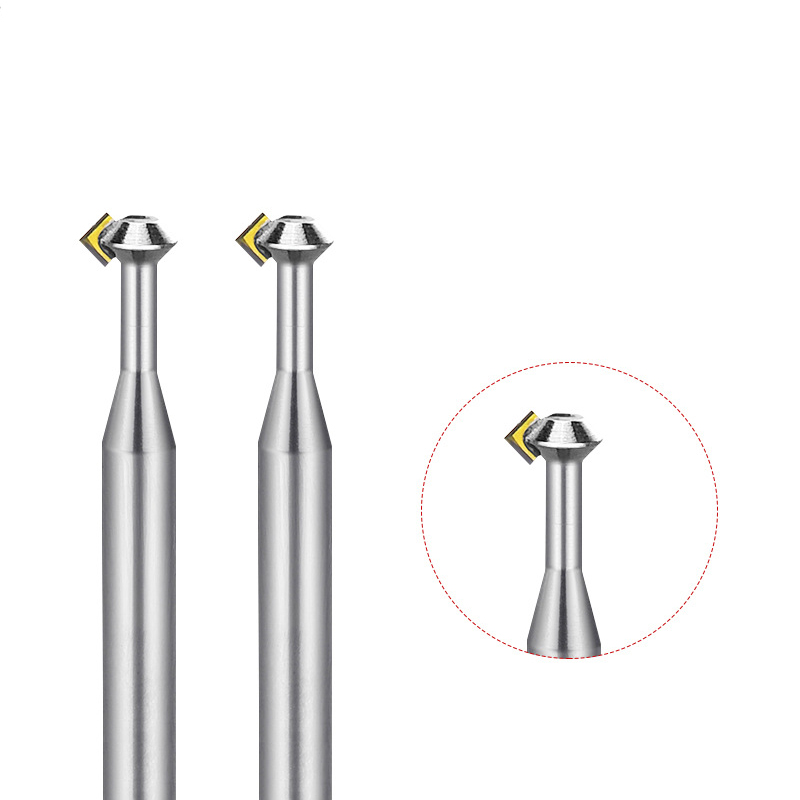
MCD High Gloss Chamfer Cutter For Gold
Product Information Origin Tianjing, China Type Flat Milling Cutter Brand Msk Whether To Coat Uncoated Series Cutter Milling Cutter Processing Range Clocks And Watches, Copp […]
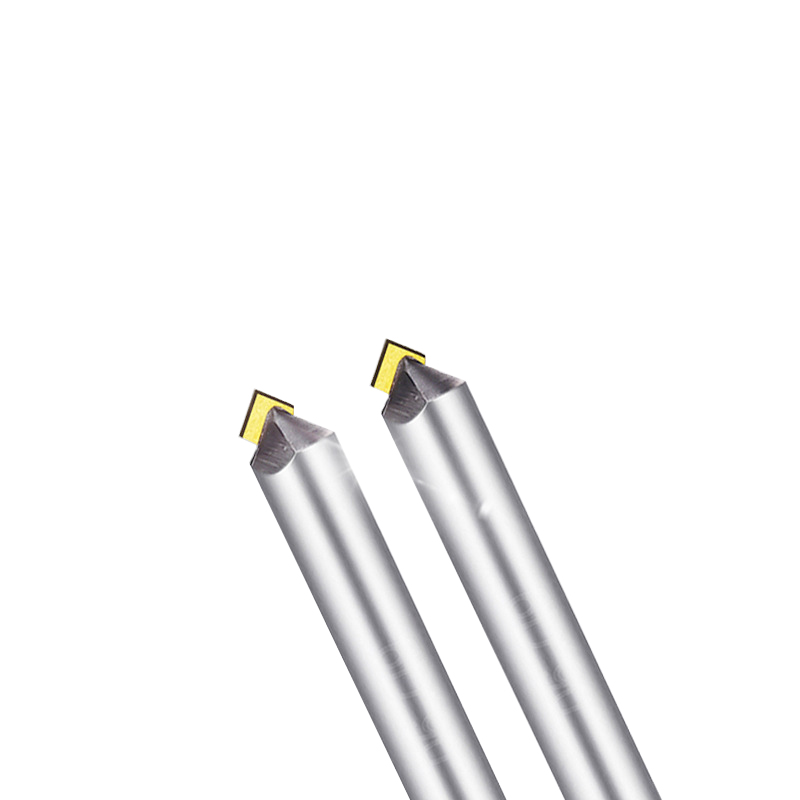
Lathe Bits MCD High Gloss Chamfer Tool
Product Information Origin Tianjing, China Cutting Edge Form Straight Edge Brand MSK Material Single Crystal Diamond Chamfer Angle 30°-180° Type Angle Milling Cutter Minimum […]
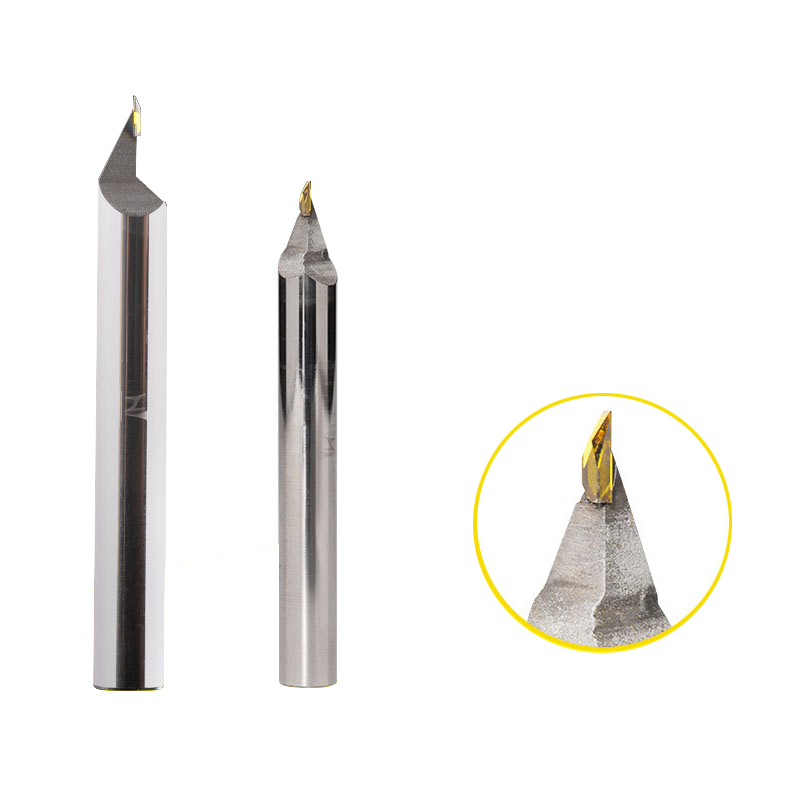
CVD/PVD/MCD Gold Jewelry Diamond Engraving Cutter
Parameter Product Name Single Crystal Diamond Carving Cutter Rotating Speed 10000-30000r/min Tool Nose Width 0.1-6.0mm Feed 1500-5000mm/min Blade Material Single Crystal Dia […]
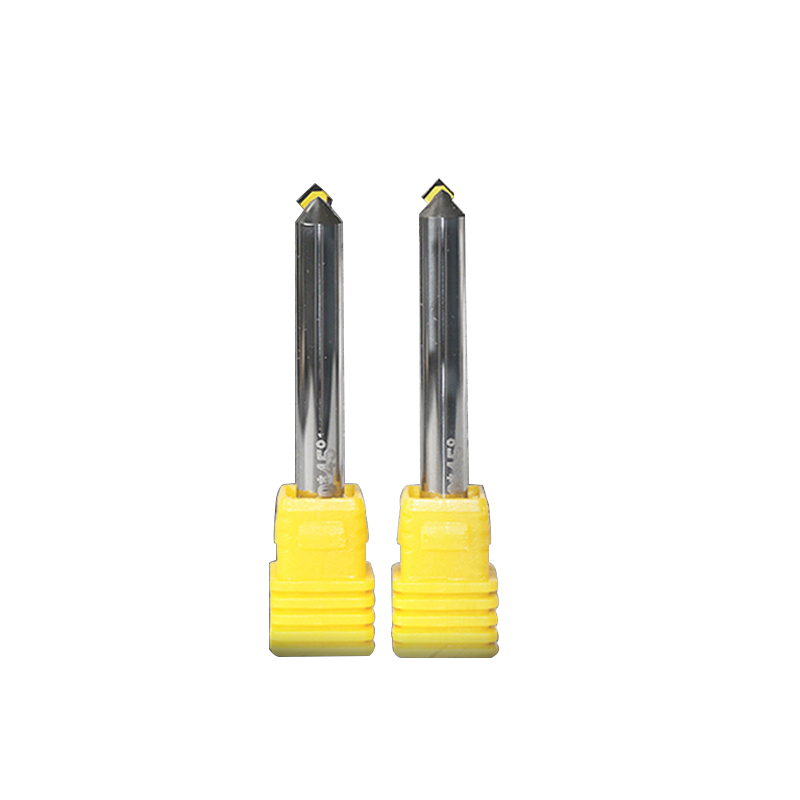
MCD Polishing Cutter for Gold Silver
Product Information Origin Tianjing, China Whether To Coat Uncoated Brand MSK Unit Weight 0.3kg Tool material Tungsten steel bar imported from Germany Product Size Shank Dia […]
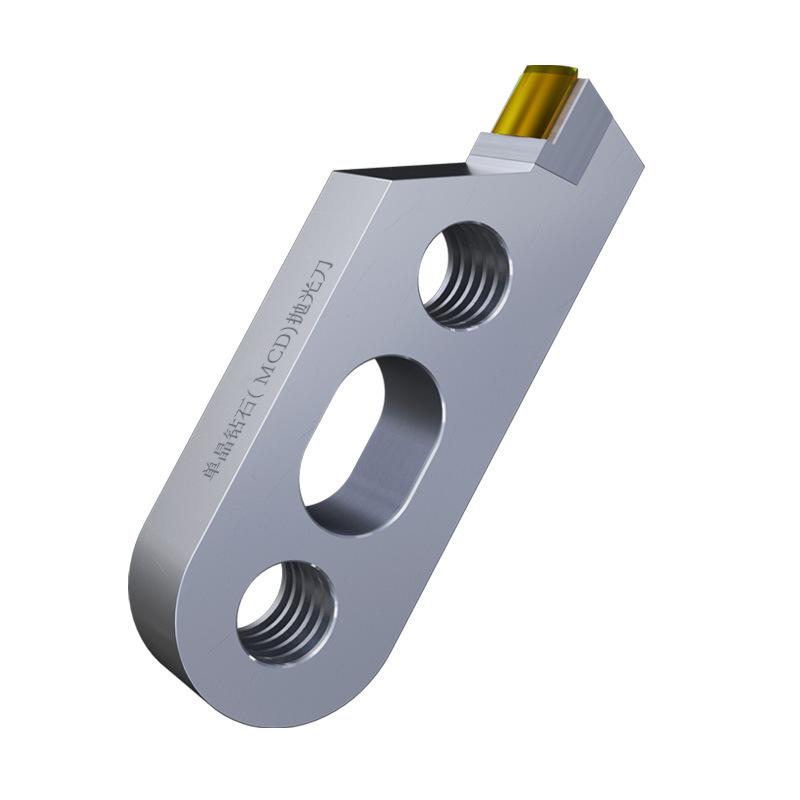
Single Crystal Diamond Polishing Cutter
Origin Tianjing, China Shank Diameter 6 (mm) Brand MSK Blade Change Method The Diamond Is Welded To The Cutter Body As A Whole Material Single Crystal Diamond (MCD) Scope Of […]
Post time: 2023-07-09