This piece of writing seeks to equip the reader, even those with negligible familiarity with PCD inserts, with the full knowledge of how to operate them.
PCD inserts are the perfect solution for machining even the toughest and most abrasive materials. Boasting one of the highest hardness levels, these tools are made with a specific type of polycrystalline diamond, an extraordinary component that is renowned for its incredible strength. PCD inserts can be utilized on various types of machining operations, ranging from milling and drilling to turning.
The cutting edge of PCD inserts is delicate and can easily be compromised, so exercise caution when handling them. Additionally, much heat is created when using these inserts, so it is recommended that they remain cooled by employing coolant or a circulating air system. Furthermore, due to the high rate of wear, these inserts necessitate frequent replacement as a matter of course.
Here are Ideas for Navigating the Use of PCD Inserts:
Selecting the suitable PCD insert is crucial, as an extensive variety of such inserts is available in the market.
The insert should serve the original, intended purpose. PCD inserts are fashioned and developed for specific machining jobs – such as turning, milling, and drilling – making sure every component fits snugly into its operational role.
For the best results while machining, one should operate PCD inserts at the optimal velocity for that particular material. Although these inserts are highly performant at high speeds, the material needs to be taken into account for using them at their maximum capacity.
Inserts should be run through the material at a steady speed that does not set off any alarms. If you move too quickly, the insert can become compromised, unable to efficiently cut its intended subjects. Conversely, a too-slow approach will bog down the operation and significantly increase overall completion time. Find the sweet spot, work at an even pace, and stay the course until you successfully achieve your desired outcome.
PCD inserts work hard and create a great deal of heat. To ensure long-term quality, they need to be maintained at a cool temperature – that’s where coolant or air comes in. Coolant or air keeps the insert at an optimal temperature, preventing it from becoming too hot, and potentially breaking.
When signs of wear are evident, it is necessary to swap out the PCD insert. Their endurance is limited, so don’t be surprised if they need to be replaced sooner rather than later.
Harnessing the power of PCD inserts allows for the machining of even the toughest and most abrasive materials with ease. If these tips are followed, you can maximize the return on your investment in PCD inserts.
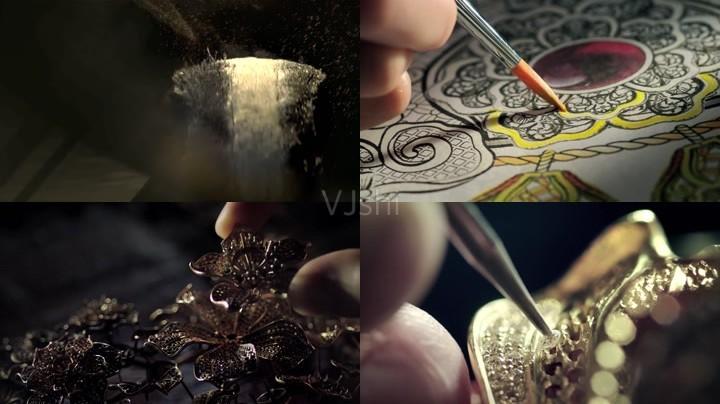
Related Product
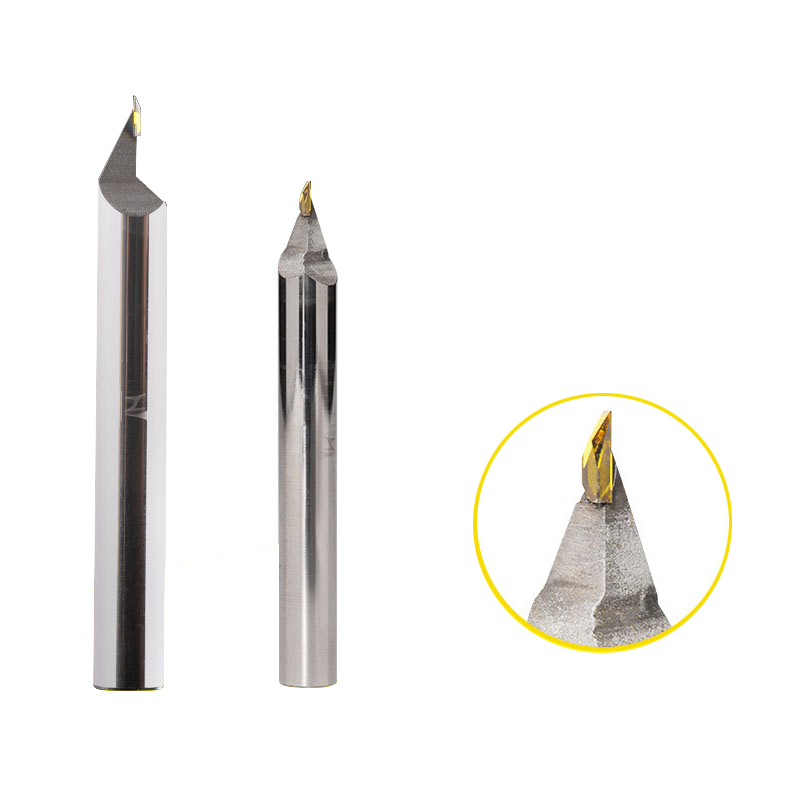
CVD/PVD/MCD Gold Jewelry Diamond Engraving Cutter
Parameter Product Name Single Crystal Diamond Carving Cutter Rotating Speed 10000-30000r/min Tool Nose Width 0.1-6.0mm Feed 1500-5000mm/min Blade Material Single Crystal Dia […]
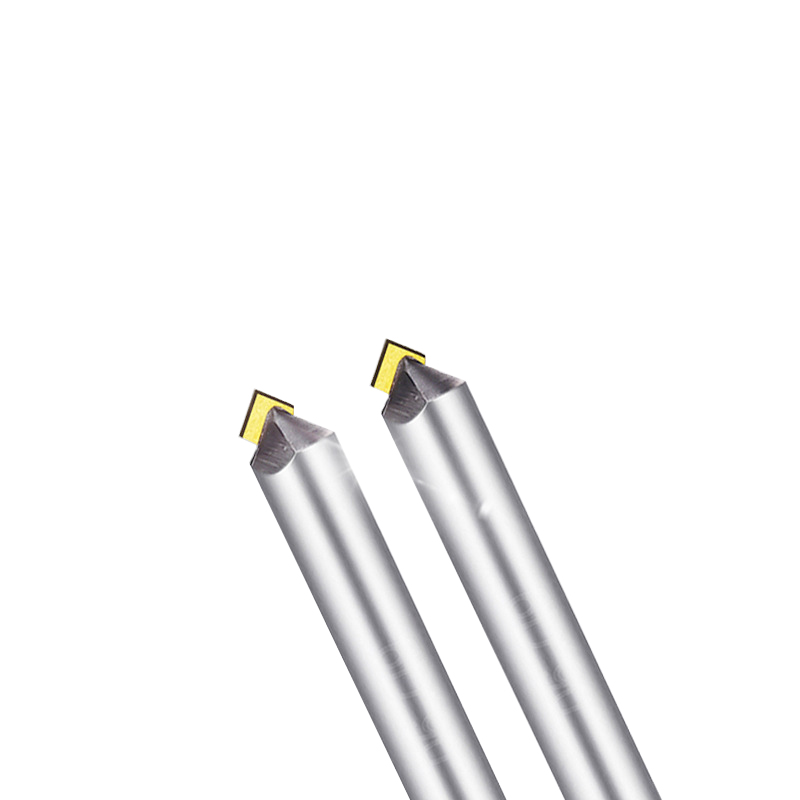
Lathe Bits MCD High Gloss Chamfer Tool
Product Information Origin Tianjing, China Cutting Edge Form Straight Edge Brand MSK Material Single Crystal Diamond Chamfer Angle 30°-180° Type Angle Milling Cutter Minimum […]
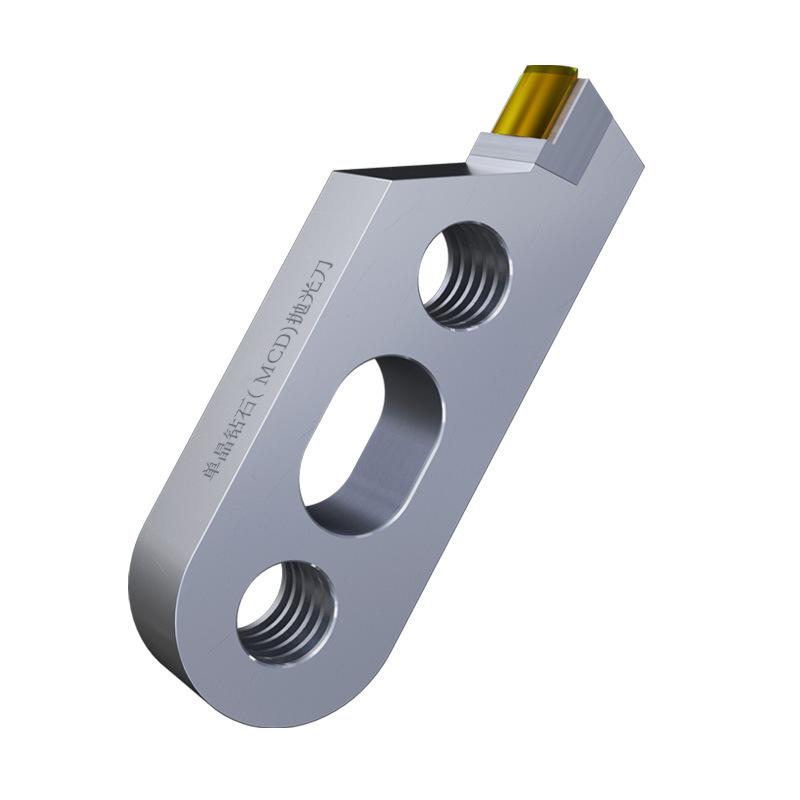
Single Crystal Diamond Polishing Cutter
Origin Tianjing, China Shank Diameter 6 (mm) Brand MSK Blade Change Method The Diamond Is Welded To The Cutter Body As A Whole Material Single Crystal Diamond (MCD) Scope Of […]
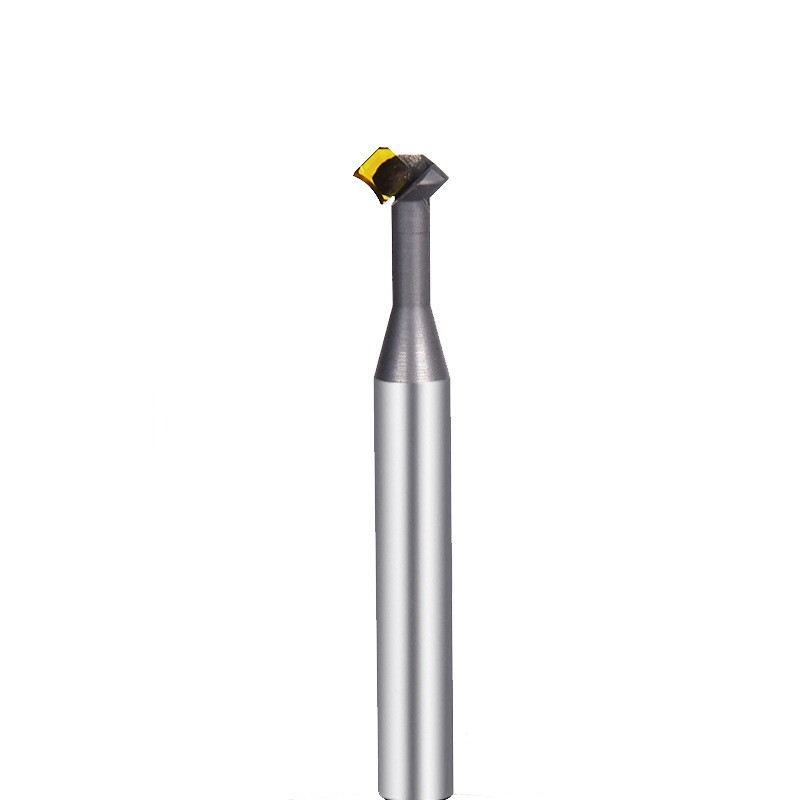
MCD Turning Tool Mirrow Finish R Cutter
Product Information Product Name Single Crystal Diamond Lower Chamfering Inner R Cutter Brand MSK Handle Material Tungsten Steel Blade Material Customized Pcd, Single Crysta […]
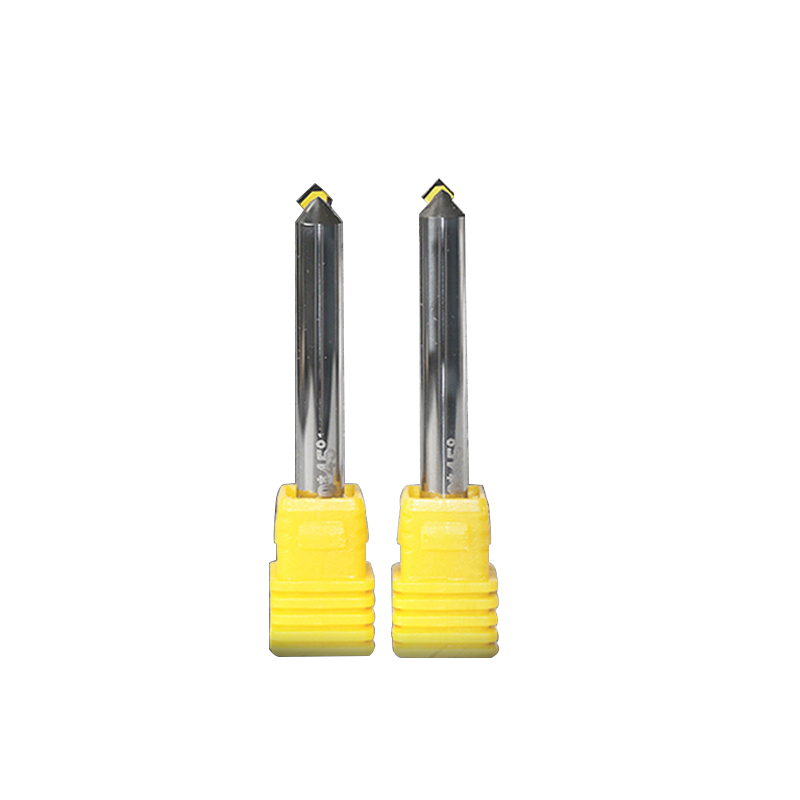
MCD Polishing Cutter for Gold Silver
Product Information Origin Tianjing, China Whether To Coat Uncoated Brand MSK Unit Weight 0.3kg Tool material Tungsten steel bar imported from Germany Product Size Shank Dia […]
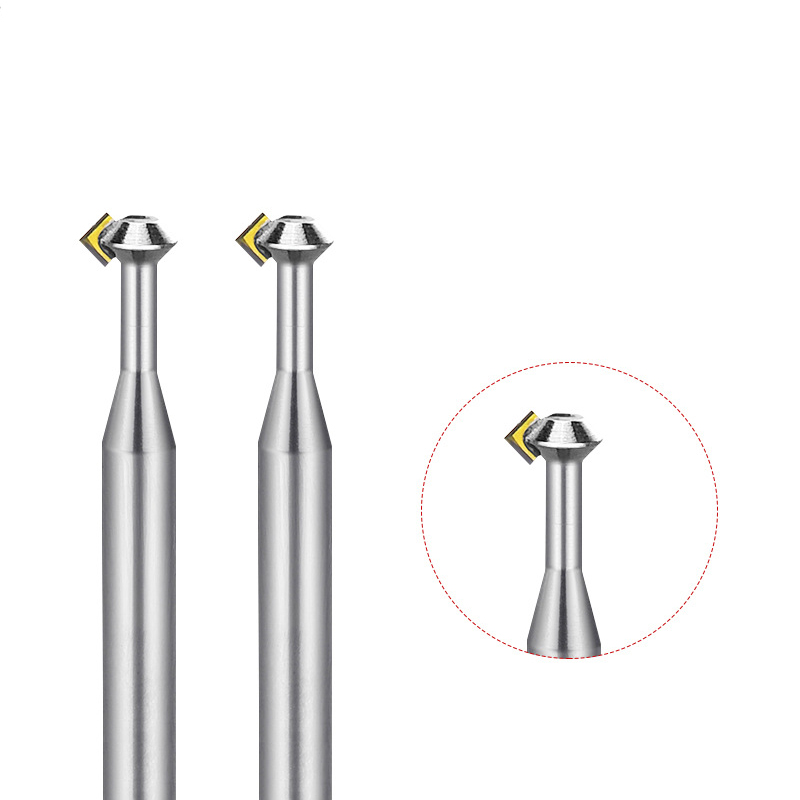
MCD High Gloss Chamfer Cutter For Gold
Product Information Origin Tianjing, China Type Flat Milling Cutter Brand Msk Whether To Coat Uncoated Series Cutter Milling Cutter Processing Range Clocks And Watches, Copp […]
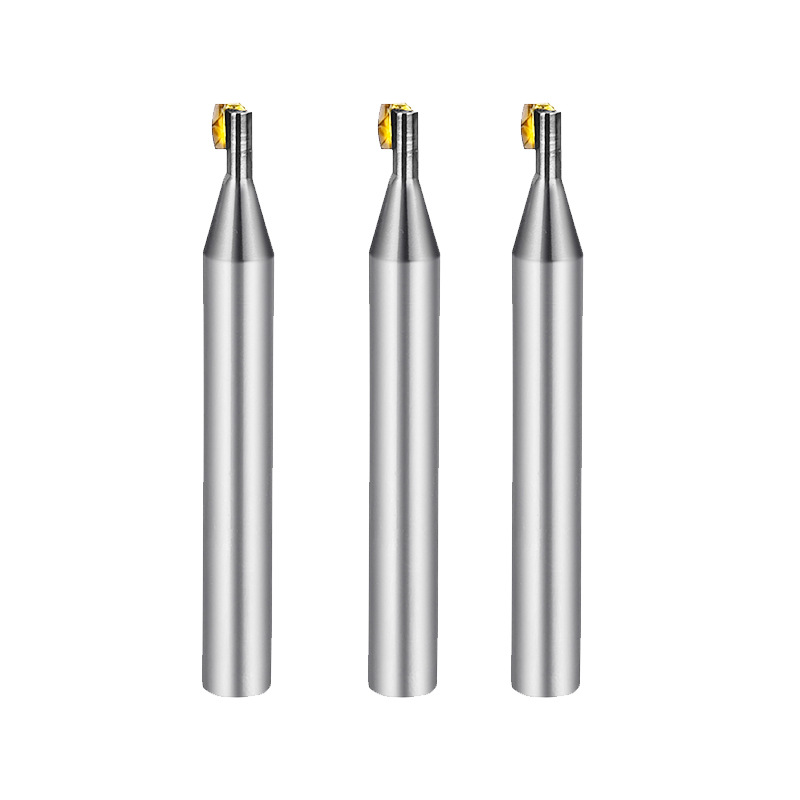
Diamond Turning Tools Outer Jewelry R Cutter
Product Information Origin Tianjing, China Material Tungsten Steel Brand Msk Type Half Round Key Milling Cutter Product Name Single Crystal Diamond Side Edge Arc Milling Cut […]
Post time: 2023-07-04