Selecting the correct PCD milling cutter for your operations may require some insight. To bolster your decision-making process, the following guidance can direct you in finding the right cutter for your venture.
1. What material is being subject to machining? 2. How tough or resilient is the material? 3. What cutting depth is to be maintained? 4. How wide will be the cut? 5. What rate of feed is documented? 6. How quickly will the cutter operate? 7. What number of flutes are needed? 8. Is there a coating on the tooling? 9. What is the tool geometry? 10. Who is the producer of the device?
When selecting a PCD milling cutter, the key element that must be taken into account is the material that needs to be carved. It is essential that the tool is capable of delicately removing material without compromising its integrity or fracturing it.
To ensure its ability to penetrate the material, the hardness of the substance is essential. It must possess strength enough to break through the surface without fail.
How Far Should the Cut Go?
Achieving an appropriate depth with the cutter is an essential element to factor in. It’s necessary to have the ability to reach one’s intended depth while also ensuring the cutter does not fracture.
The Breadth of Clearing
Arriving at the desired width is a key consideration for the cutter. It must be able to move to that point without risk of fragmentation.
Digesting the Proper Amount: Utilizing Feed Rate
Swiftly traversing through the material, the cutter depends on a steady feed rate to ensure it can reach the required depth and breadth without any damage.
Cutter Velocity: How Quickly is the Cut?
The cutting action of the rotator requires an optimal rate of spin to incrementally plough through the material without fracturing. When gauged correctly, the rate of circulation triggers a force that can be finely tuned to accomplish the desired penetrating depth and expanse.
Magnitude of Flutes
The flutes on the cutter indicate how many cutting edges it possesses. The more of these veins, the smoother and more rapid it is able to carve through surfaces.
A cutter’s durability and efficiency relies on the appropriate coating. To ensure it can glaze effortlessly through any material, the covering needs to be especially resilient.
The shape of the cutting edge is determined by the geometry of the cutter, which must be properly crafted to suit the material it will be slicing through.
When considering which cutter to purchase, it is important to make sure the brand reputation is trustworthy. A warranty should also be included with the product to ensure peace of mind when making the investment.
Related Product
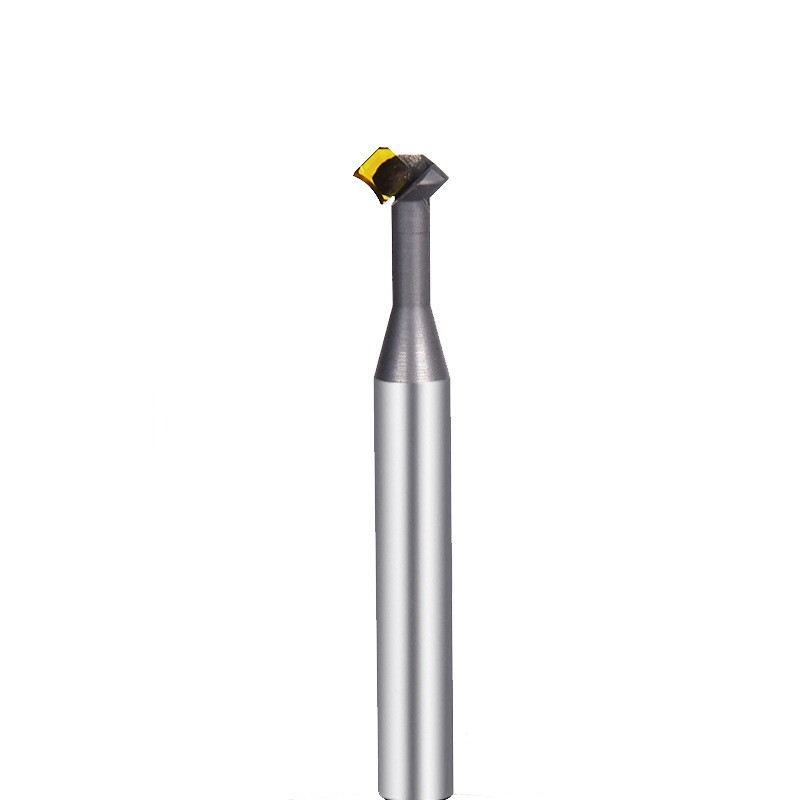
MCD Turning Tool Mirrow Finish R Cutter
Product Information Product Name Single Crystal Diamond Lower Chamfering Inner R Cutter Brand MSK Handle Material Tungsten Steel Blade Material Customized Pcd, Single Crysta […]
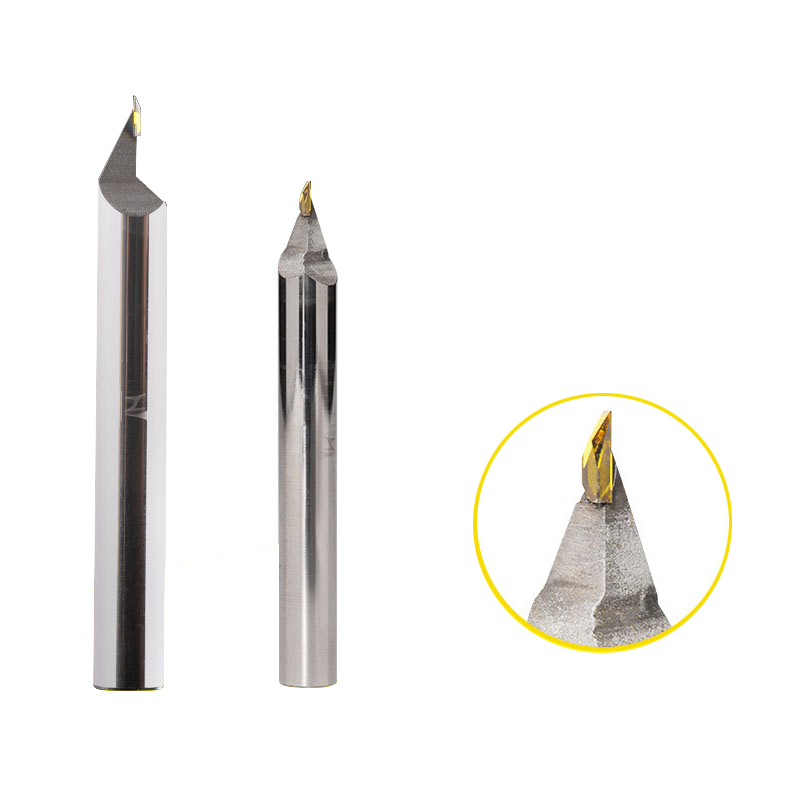
CVD/PVD/MCD Gold Jewelry Diamond Engraving Cutter
Parameter Product Name Single Crystal Diamond Carving Cutter Rotating Speed 10000-30000r/min Tool Nose Width 0.1-6.0mm Feed 1500-5000mm/min Blade Material Single Crystal Dia […]
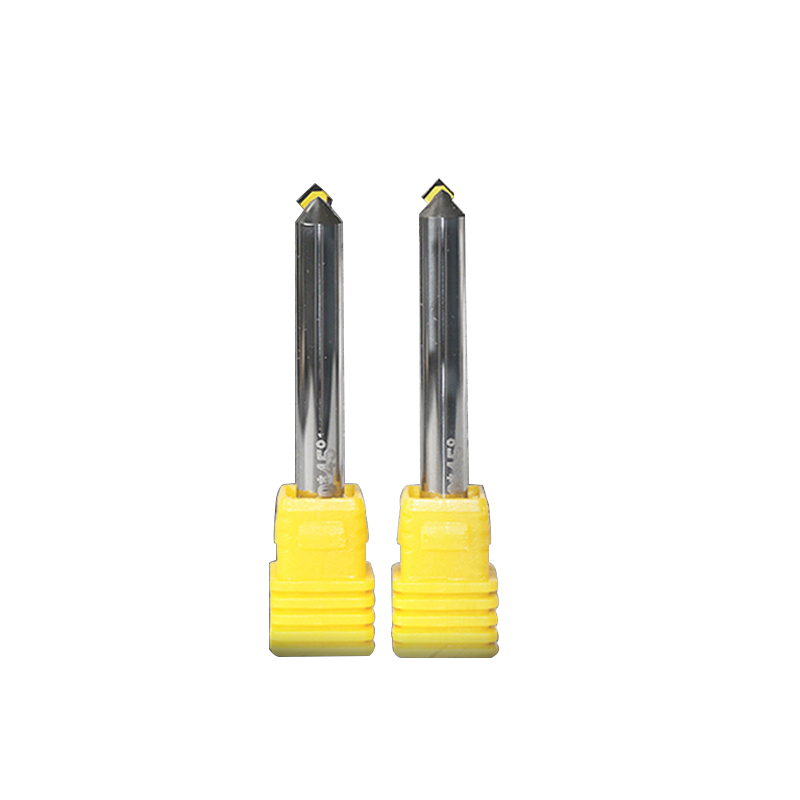
MCD Polishing Cutter for Gold Silver
Product Information Origin Tianjing, China Whether To Coat Uncoated Brand MSK Unit Weight 0.3kg Tool material Tungsten steel bar imported from Germany Product Size Shank Dia […]
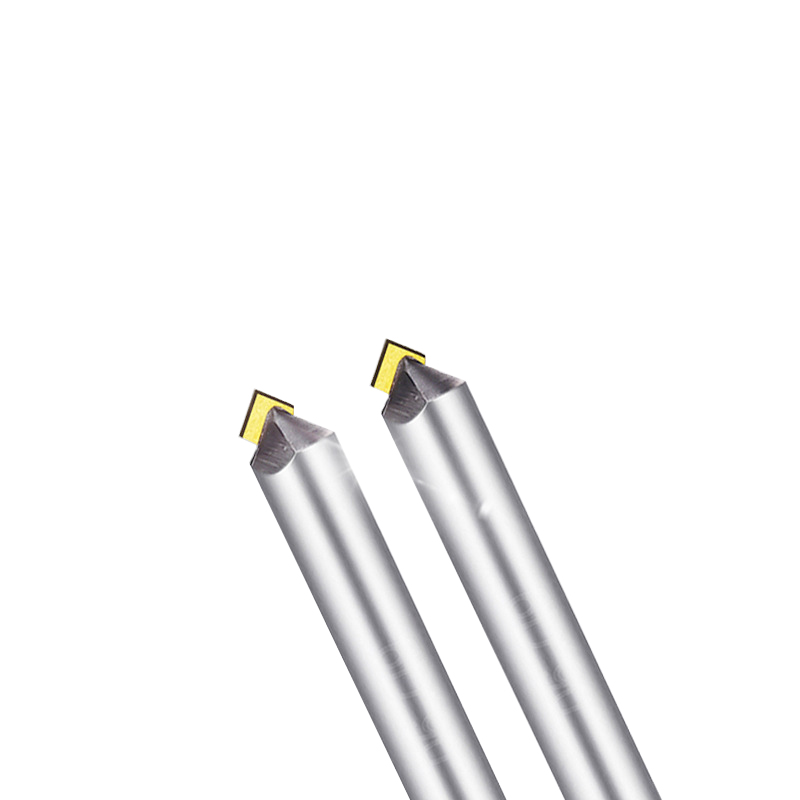
Lathe Bits MCD High Gloss Chamfer Tool
Product Information Origin Tianjing, China Cutting Edge Form Straight Edge Brand MSK Material Single Crystal Diamond Chamfer Angle 30°-180° Type Angle Milling Cutter Minimum […]
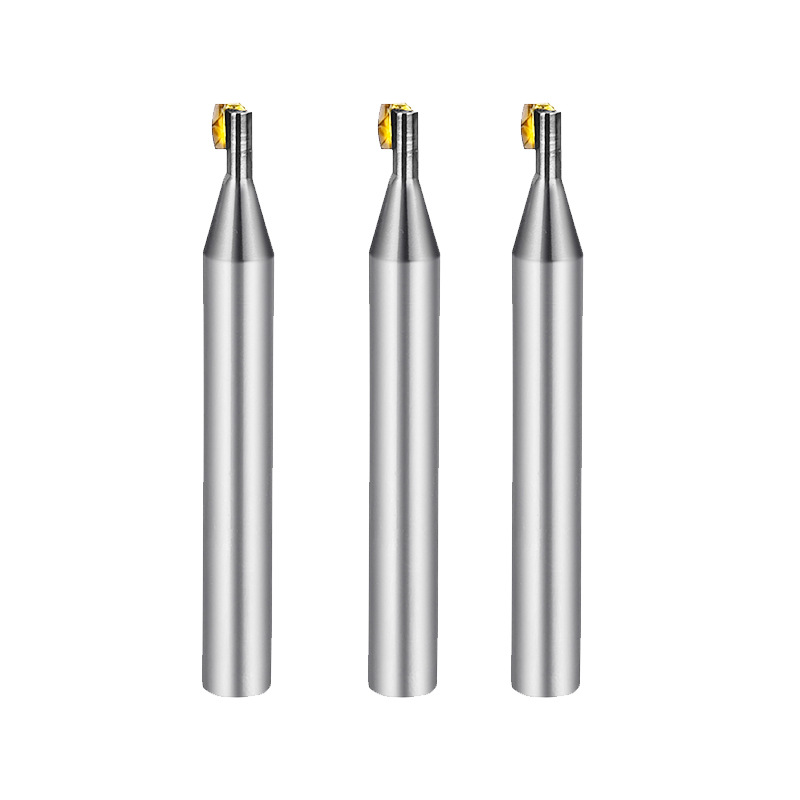
Diamond Turning Tools Outer Jewelry R Cutter
Product Information Origin Tianjing, China Material Tungsten Steel Brand Msk Type Half Round Key Milling Cutter Product Name Single Crystal Diamond Side Edge Arc Milling Cut […]
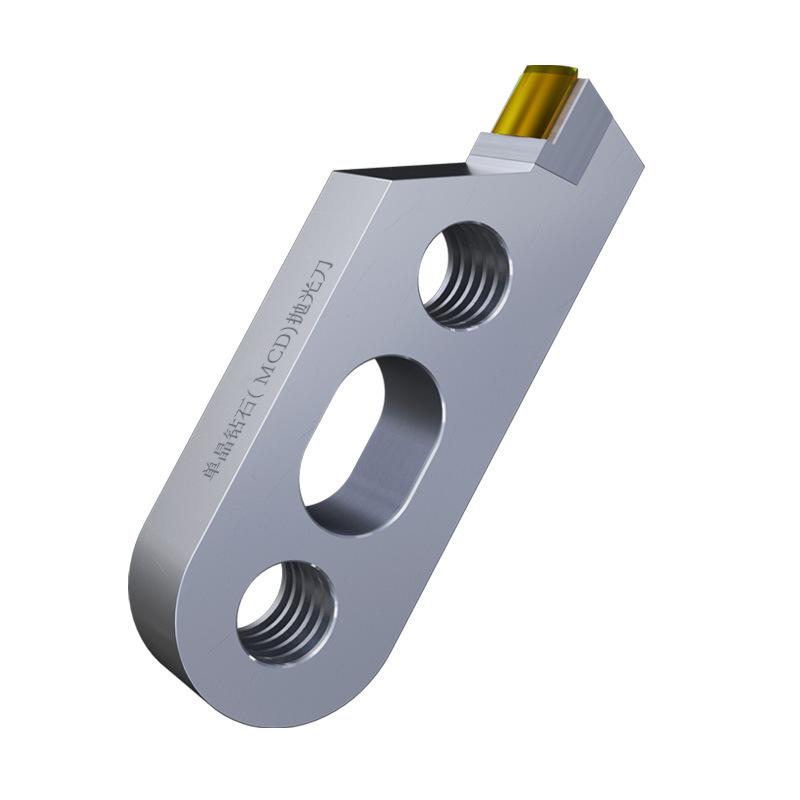
Single Crystal Diamond Polishing Cutter
Origin Tianjing, China Shank Diameter 6 (mm) Brand MSK Blade Change Method The Diamond Is Welded To The Cutter Body As A Whole Material Single Crystal Diamond (MCD) Scope Of […]
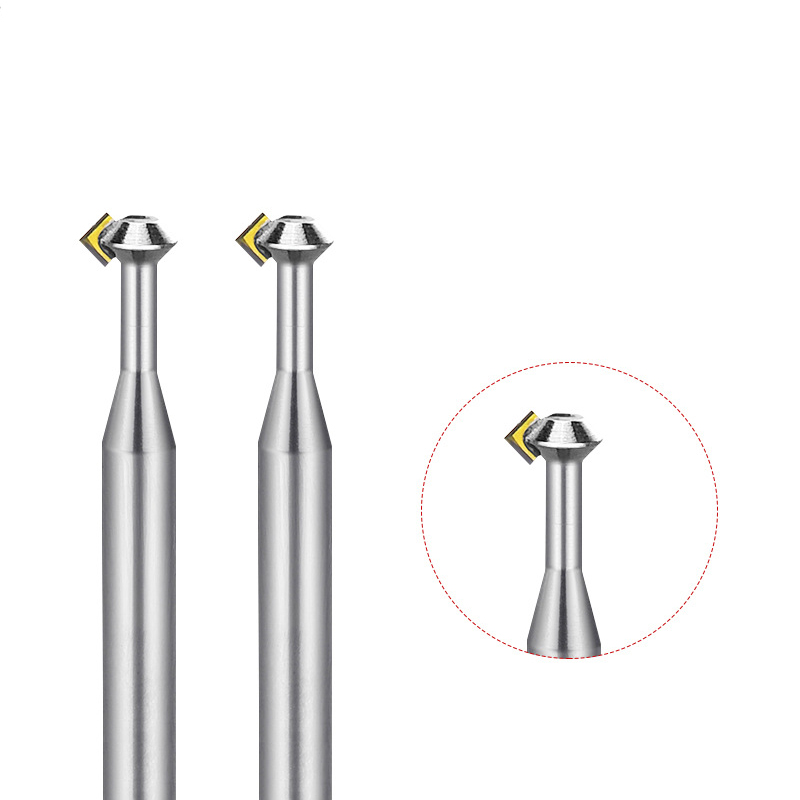
MCD High Gloss Chamfer Cutter For Gold
Product Information Origin Tianjing, China Type Flat Milling Cutter Brand Msk Whether To Coat Uncoated Series Cutter Milling Cutter Processing Range Clocks And Watches, Copp […]
Post time: 2023-06-15