When it comes to machining non-ferrous metals and composites, PCD inserts have become the preferred tools for many individuals. Still, there is a seemingly endless variety of PCD inserts available, and deciding on one that’s right for you can be a daunting task.
As you consider which PCD insert to purchase, four pertinent factors cannot be overlooked: the type of material you intend to work with, its hardness characteristics, the depth of cut, and the feed rate. Exploring each of these components in greater detail is essential. To begin, you must determine what type of material is involved in machining.
When selecting PCD inserts, the material which is going to be machined is of vital importance. That’s because each material necessitates a distinct kind of insert.
Machining aluminum requires the use of a tungsten carbide insert containing a PCD tip, due to this insert’s capability to withstand the powerful temperatures created from the task.
PCD tips installed on inserts fashioned from cobalt or high-speed steel can provide the protection necessary to permit machining of steel – they can tolerate the substantial heat and erosion that come with the task.
The indomitable nature of the substance or material in question is most definitely notable. Its unfaltering strength and seeming invincibility can be attributed to the material’s remarkable hardness.
When selecting PCD inserts, the hardness of the material necessitates a need for an insert that is similarly resistant. Choose inserts whose quality adheres to the hardness of the material itself.
Unquestionably, to successfully work with soft materials such as aluminum, employing an insert produced from tungsten carbide with a PCD tip is paramount. This special type of insert is made with the expectation that it will be able to handle the very high temperatures created while machining aluminum.
Machining hard materials, such as steel, requires an insert constructed from cobalt or HSS with a PCD tip, as they are able to resist the heat and abrasion produced during the machining procedure.
The Profundity of the Penknife Cut
For deep machining, selecting the proper PCD insert is paramount. As the depth of a cut increases, the hardness and durability of the insert must follow suit.
If your machining task involves a shallow cut, then you should opt for an insert fabricated with tungsten carbide and furnished with a PCD tip. This kind of insert has been especially designed to hold up against the extremely high temperature generated when machining aluminum.
To make a deep cut, it is imperative to choose an insert crafted from cobalt or high-speed steel with a PCD tip. This option can withstand the temperature and strain associated with machining steel, thus providing a reliable and efficient solution.
4. Intake Velocity – The Rate at Which Nourishment is Consumed
The velocity at which the cutting tool is passed through the material is known as the feed rate, denoted in inches per minute (ipm).
When selecting PCD inserts, the feed rate is a critical component to consider, as it impacts the time that the insert is in contact with the material. Utilising a faster feed rate decreases the amount of time the insert engages with the medium, thus reducing wear.
When the feed rate is decreased, the insert continues in contact with the material for a prolonged period, leading to increased wear and tear.
Armed with knowledge of the four elements necessary to pick the optimal PCD insert, the process of selecting the perfect fit for your project can be narrowed down, allowing you to select the most suitable one.
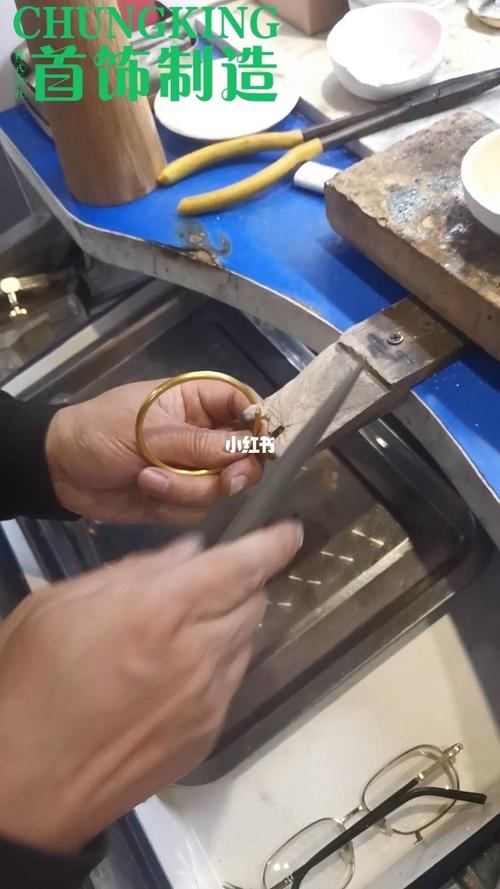
Related Product
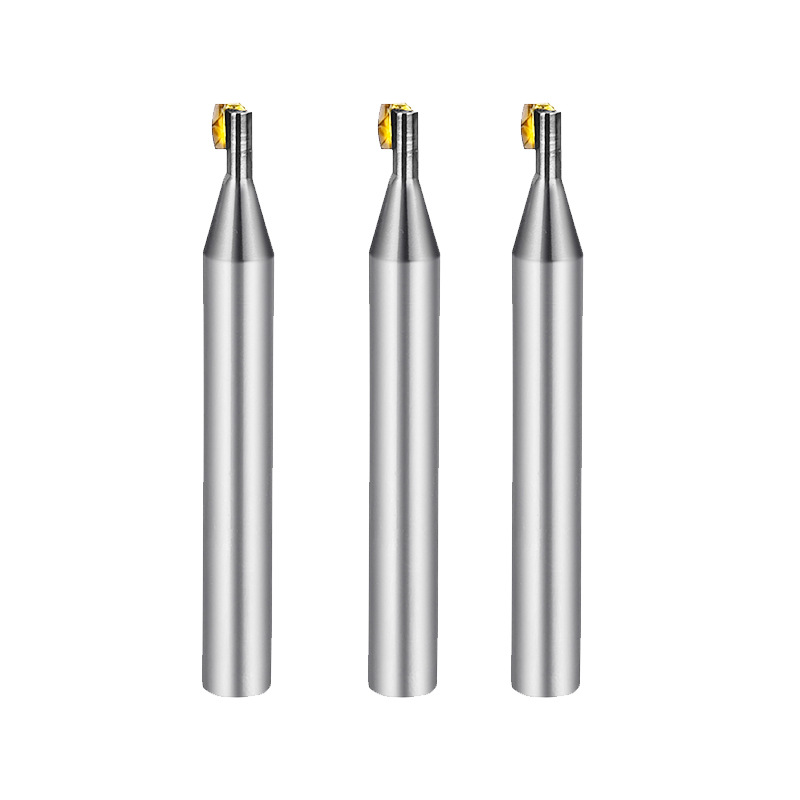
Diamond Turning Tools Outer Jewelry R Cutter
Product Information Origin Tianjing, China Material Tungsten Steel Brand Msk Type Half Round Key Milling Cutter Product Name Single Crystal Diamond Side Edge Arc Milling Cut […]
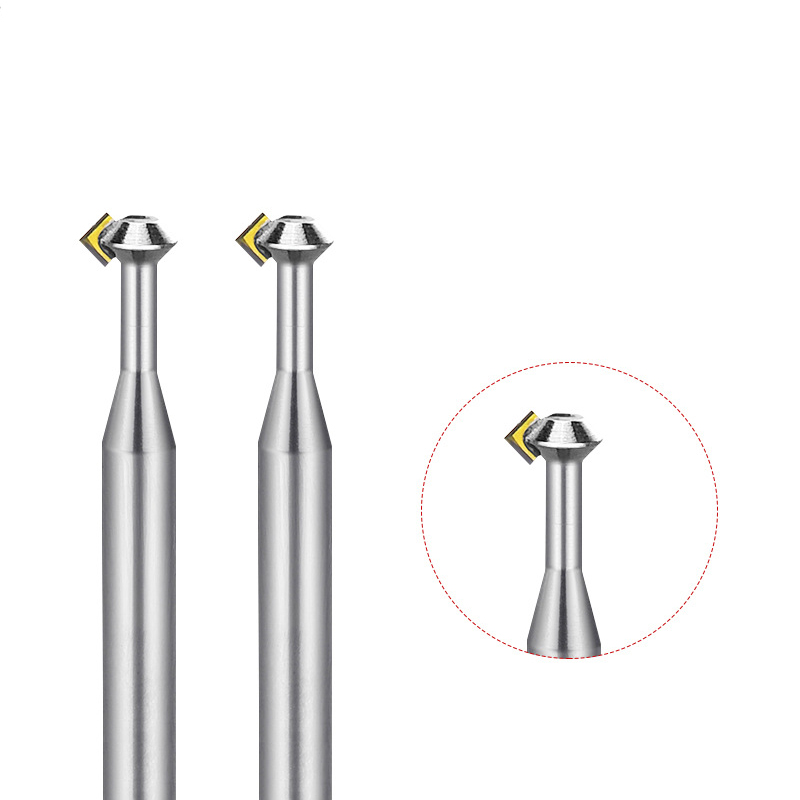
MCD High Gloss Chamfer Cutter For Gold
Product Information Origin Tianjing, China Type Flat Milling Cutter Brand Msk Whether To Coat Uncoated Series Cutter Milling Cutter Processing Range Clocks And Watches, Copp […]
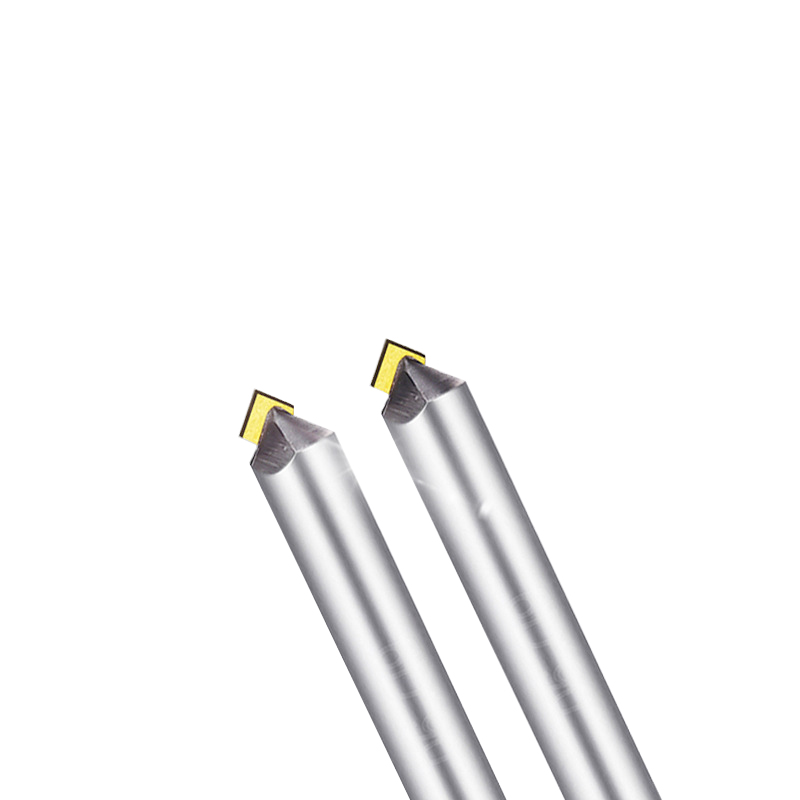
Lathe Bits MCD High Gloss Chamfer Tool
Product Information Origin Tianjing, China Cutting Edge Form Straight Edge Brand MSK Material Single Crystal Diamond Chamfer Angle 30°-180° Type Angle Milling Cutter Minimum […]
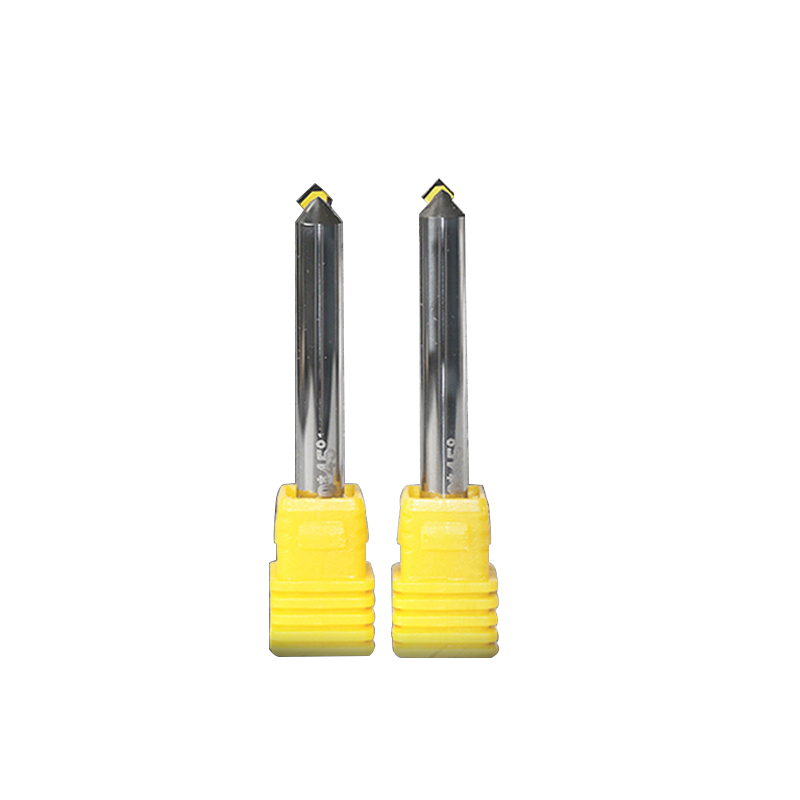
MCD Polishing Cutter for Gold Silver
Product Information Origin Tianjing, China Whether To Coat Uncoated Brand MSK Unit Weight 0.3kg Tool material Tungsten steel bar imported from Germany Product Size Shank Dia […]
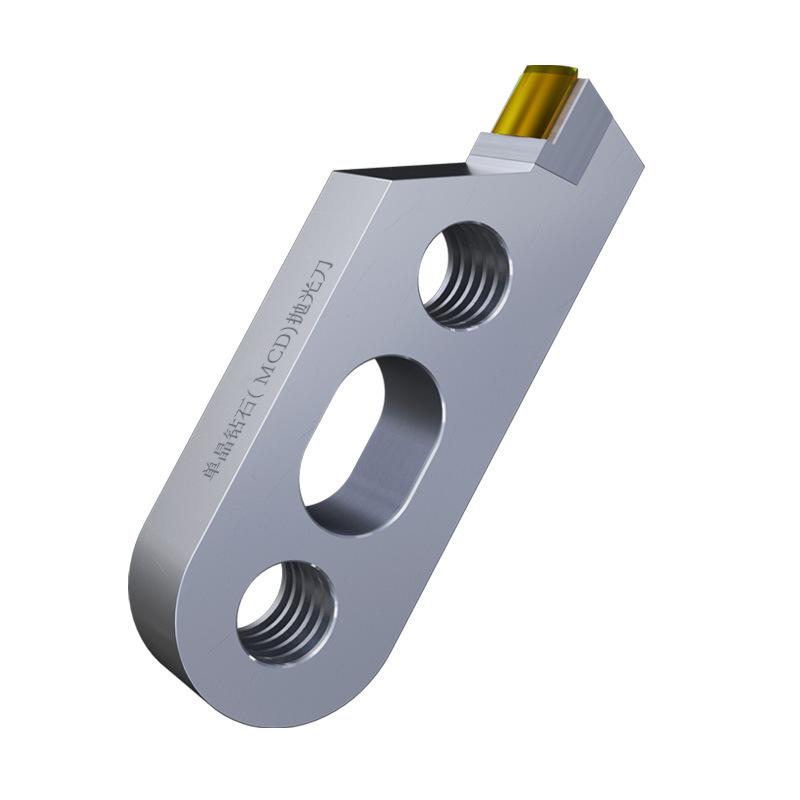
Single Crystal Diamond Polishing Cutter
Origin Tianjing, China Shank Diameter 6 (mm) Brand MSK Blade Change Method The Diamond Is Welded To The Cutter Body As A Whole Material Single Crystal Diamond (MCD) Scope Of […]
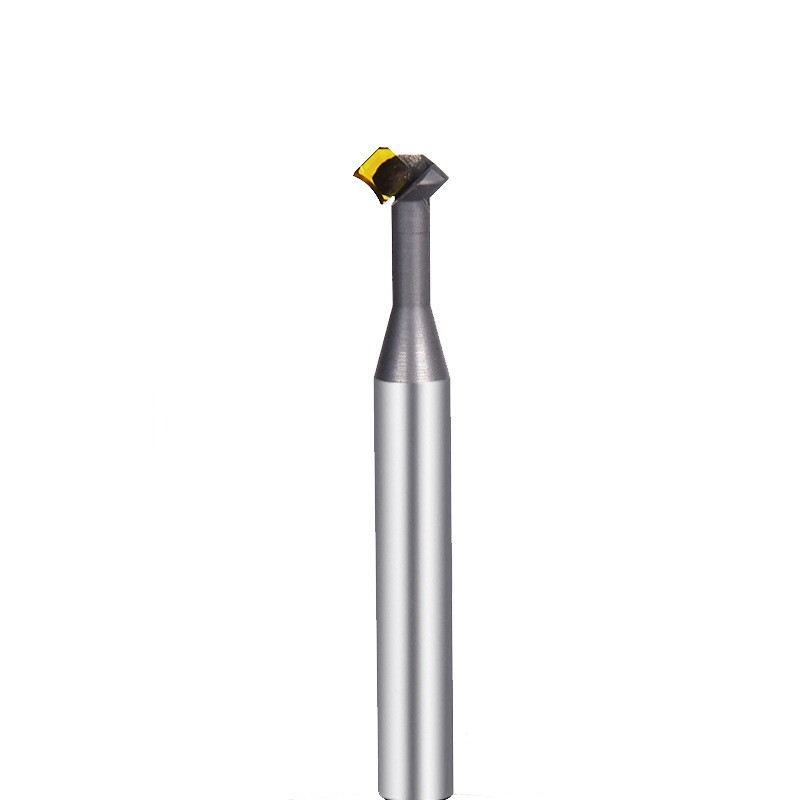
MCD Turning Tool Mirrow Finish R Cutter
Product Information Product Name Single Crystal Diamond Lower Chamfering Inner R Cutter Brand MSK Handle Material Tungsten Steel Blade Material Customized Pcd, Single Crysta […]
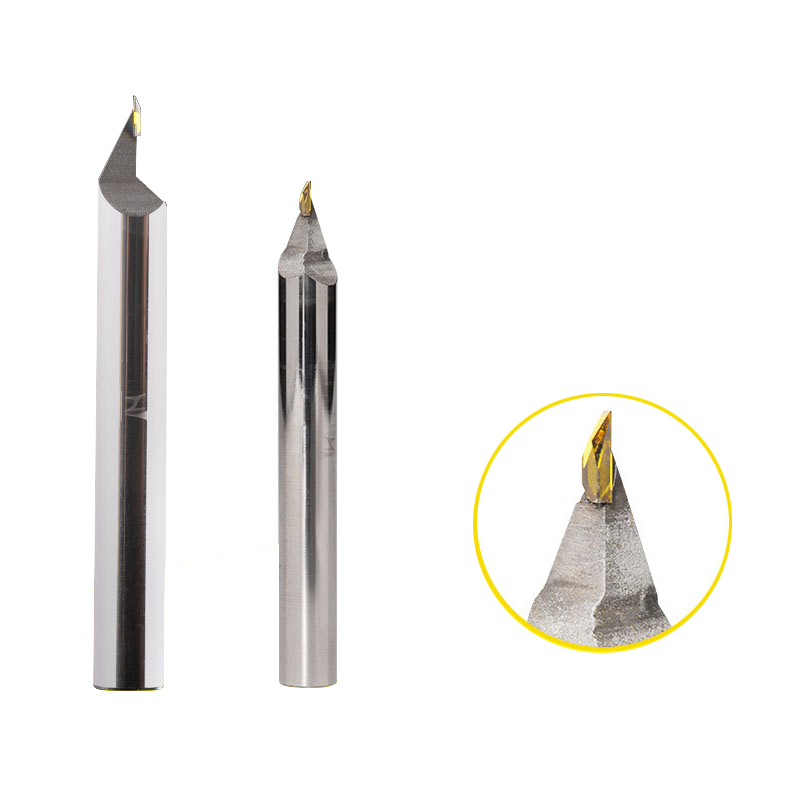
CVD/PVD/MCD Gold Jewelry Diamond Engraving Cutter
Parameter Product Name Single Crystal Diamond Carving Cutter Rotating Speed 10000-30000r/min Tool Nose Width 0.1-6.0mm Feed 1500-5000mm/min Blade Material Single Crystal Dia […]
Post time: 2023-07-10