Diamond impregnated cutters are designed to work wonders when it comes to cutting objects from hard materials with utmost precision and accuracy. From aircraft parts to medical devices and electronic components, these tools prove their worth in various industries.
To craft diamond impregnated cutters, the engineers employ a multifaceted approach that encompasses the chemical and mechanical domains. The first step is to join the diamond powder to the blade of the cutting instrument, a process called chemical vapor deposition (CVD). Then, a durable amalgam is developed by blending the diamond particles with a metallic support material such as tungsten carbide. The result is a robust composite capable of bearing extreme temperatures and tremendous forces.
After its diamond application, the cutter undergoes a transformation through mechanical abrasion – purging away any extraneous material or gunk and leaving a sleek, even cutting edge. The newly fashioned surface is then sealed with a coating to guard against future rusting and deterioration.
Prepared for operation, the diamond infused cutter is a dynamic tool able to slice through a host of substances, such as aluminum, steel, titanium and other metals as well as plastics and composites. This handy tool has become integral in the production of countless aeronautic and automotive parts, medical implements and electronic segments.
Diamond impregnated cutters offer many perks, from accuracy and precision, to the ability to move through different materials. This can help minimize product flaws and amount of time a job takes. Further, they are known for being exceptionally durable and even reusable.
Diamond impregnated cutters may be worthwhile investments, yet there are several drawbacks to keep in mind. Initially, these items are expensive, and then further costs arise due to the need for specialized equipment and personnel who have the expertise to use them. Additionally, regular upkeep including sharpening must be performed; otherwise, the blades will become dull and decrease their usefulness.
Despite their drawbacks, diamond-embedded cutters remain a highly valued resource for many industries. Their pinpoint accuracy and capacity to shape a range of supplies make them indispensable for those in need of tidy, precise cuts. Moreover, they offer a quick solution to trimming even the most tough materials.
A staple in industries for decades, diamond impregnated cutters are a one-of-a-kind tool. Taking diamond particles and bonding them to either a metal substrate or polymer matrix, they are a powerhouse cutter used for many applications – from milling and grinding to drilling, boring, and cutting.
Diamond impregnated cutters are widely sought for their sheer strength and robustness. Known to be the strongest of all natural materials, diamonds are bonded to the substrate with a mixture of metal or polymer. This creates an exceptionally hard cutting tool which can withstand rigorous use without losing its edge or sharpness. Consequently, these cutters provide a great long-term solution for grinding and cutting applications.
With its powerful diamond impregnation, these remarkable cutters can tackle seemingly impossible tasks: from slicing through hard materials such as glass and ceramics to honing metals with ease. These exceptional capabilities make the cutters suitable for a broad lineup of industries – spanning from automotive to medical and even aerospace.
Diamond impregnated cutters are a tremendous success owing to their versatility. This allows them to be used in many distinct industries, thereby slashing the cost of fabrication. Especially for small-scale producers, this is an enormous advantage as they tend to have a limited array of options when it comes to cutting tools.
Once the cutting process begins, the diamond-embedded blade undergoes a relatively straightforward assembly. The diamond and base material – which may be either metallic or polymer – are positioned in proximity with one another as heat is applied to fuse them together. After reaching a high temperature, the substrate is ready to send its shiny diamond facets into action.
End mills are the most popular type of diamond-embedded cutter, most commonly used for milling and drilling operations. The diamond particles are securely mounted to the shaft, or end, of the mill, forming a sharpened edge which slices effortlessly through materials like wood, metal, or plastic.
Want a cutting tool that is both strong and won’t break your budget? Look no further than diamond impregnated cutters! These powerful tools are perfect for a broad range of industrial applications – they’re able to slice through all kinds of materials and are surprisingly affordable to manufacture. Whether you need a trustworthy cutting implement for your large scale operations or something economical for smaller tasks, diamond impregnated cutters may be the best choice.
Related Product
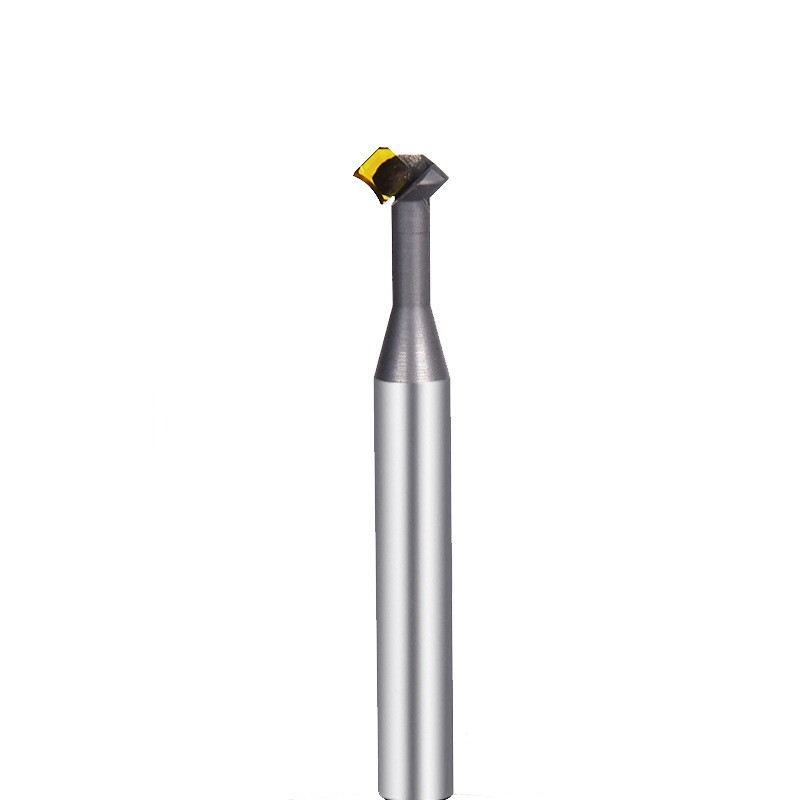
MCD Turning Tool Mirrow Finish R Cutter
Product Information Product Name Single Crystal Diamond Lower Chamfering Inner R Cutter Brand MSK Handle Material Tungsten Steel Blade Material Customized Pcd, Single Crysta […]
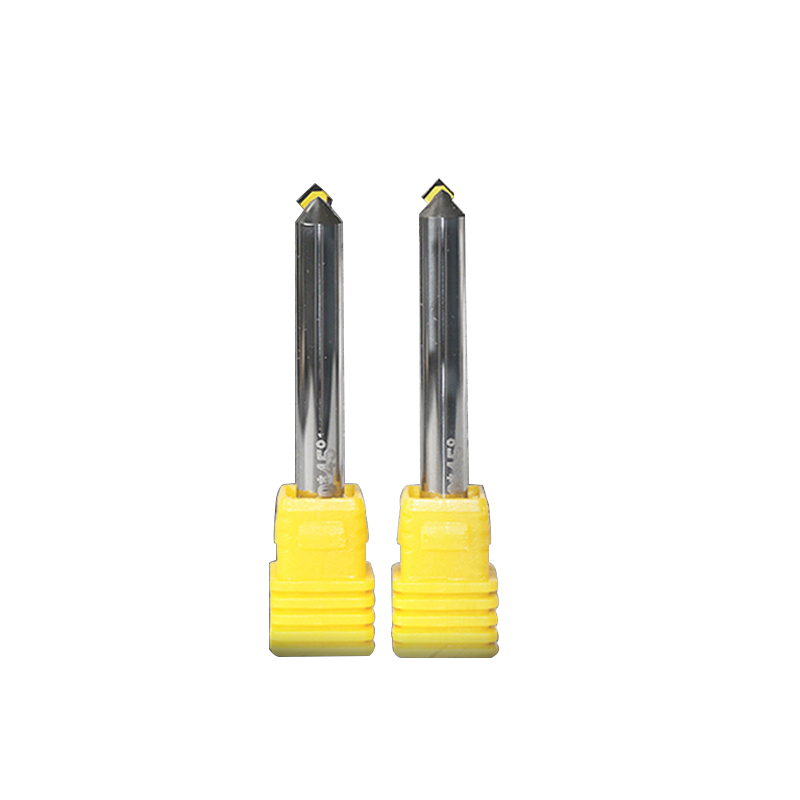
MCD Polishing Cutter for Gold Silver
Product Information Origin Tianjing, China Whether To Coat Uncoated Brand MSK Unit Weight 0.3kg Tool material Tungsten steel bar imported from Germany Product Size Shank Dia […]
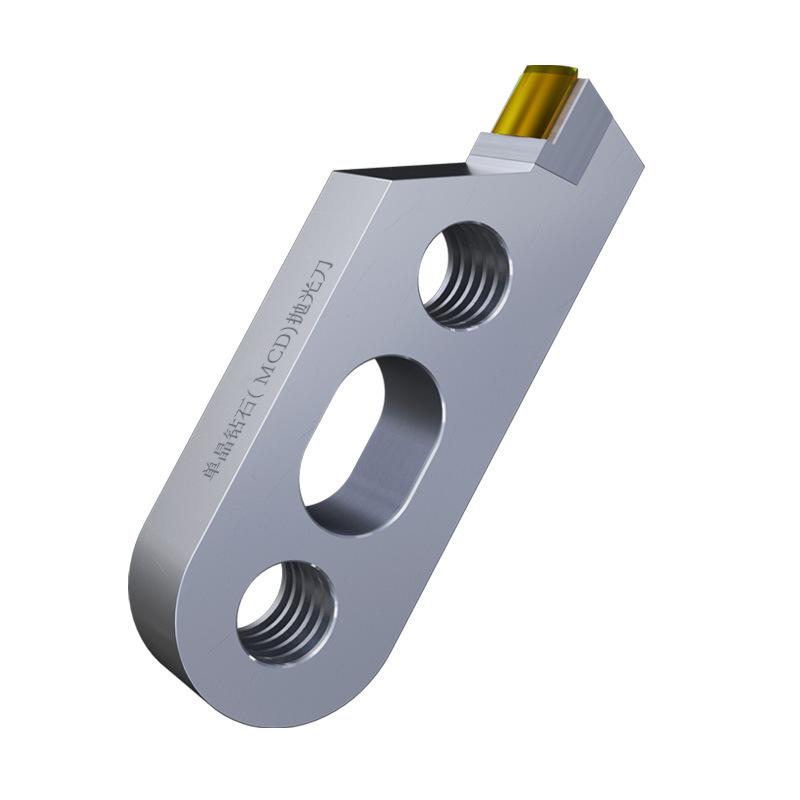
Single Crystal Diamond Polishing Cutter
Origin Tianjing, China Shank Diameter 6 (mm) Brand MSK Blade Change Method The Diamond Is Welded To The Cutter Body As A Whole Material Single Crystal Diamond (MCD) Scope Of […]
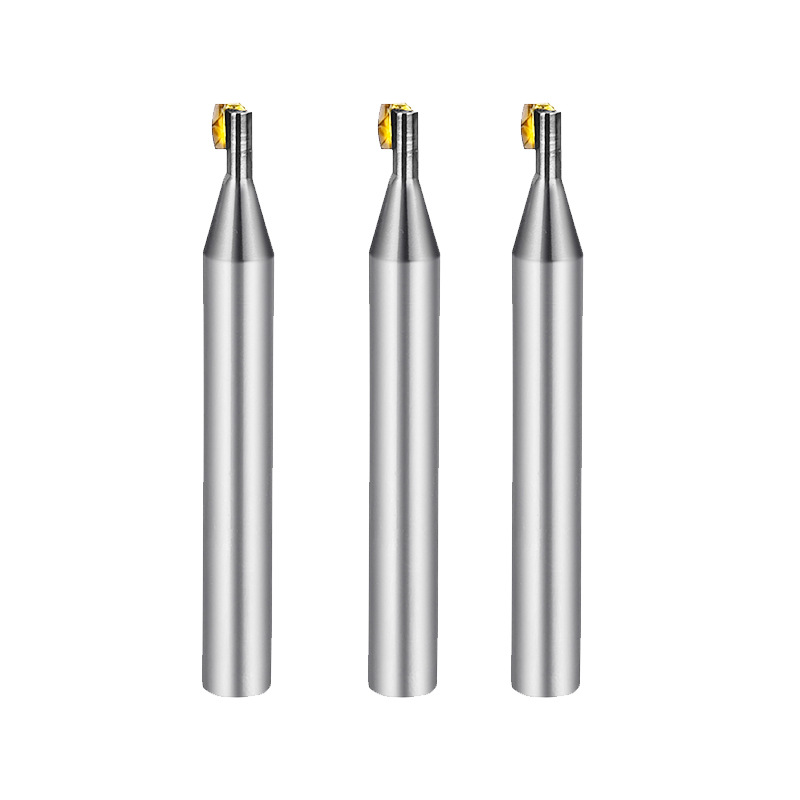
Diamond Turning Tools Outer Jewelry R Cutter
Product Information Origin Tianjing, China Material Tungsten Steel Brand Msk Type Half Round Key Milling Cutter Product Name Single Crystal Diamond Side Edge Arc Milling Cut […]
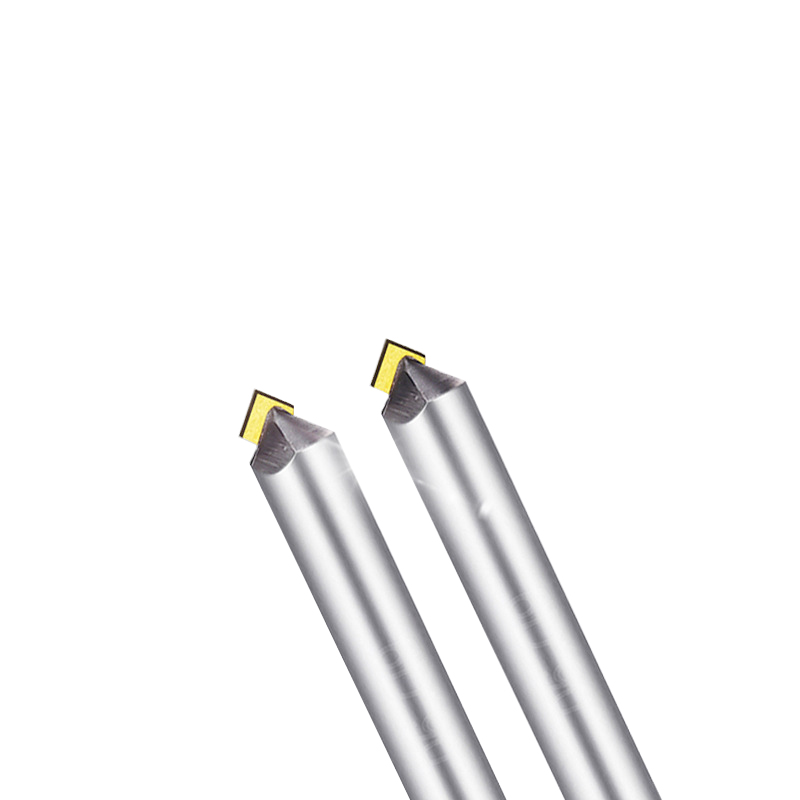
Lathe Bits MCD High Gloss Chamfer Tool
Product Information Origin Tianjing, China Cutting Edge Form Straight Edge Brand MSK Material Single Crystal Diamond Chamfer Angle 30°-180° Type Angle Milling Cutter Minimum […]
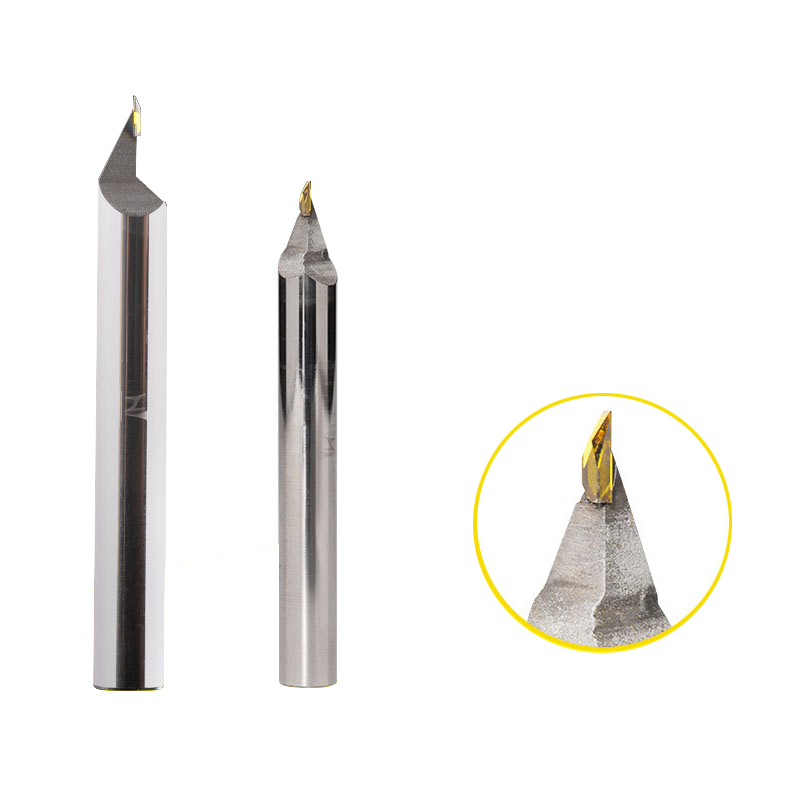
CVD/PVD/MCD Gold Jewelry Diamond Engraving Cutter
Parameter Product Name Single Crystal Diamond Carving Cutter Rotating Speed 10000-30000r/min Tool Nose Width 0.1-6.0mm Feed 1500-5000mm/min Blade Material Single Crystal Dia […]
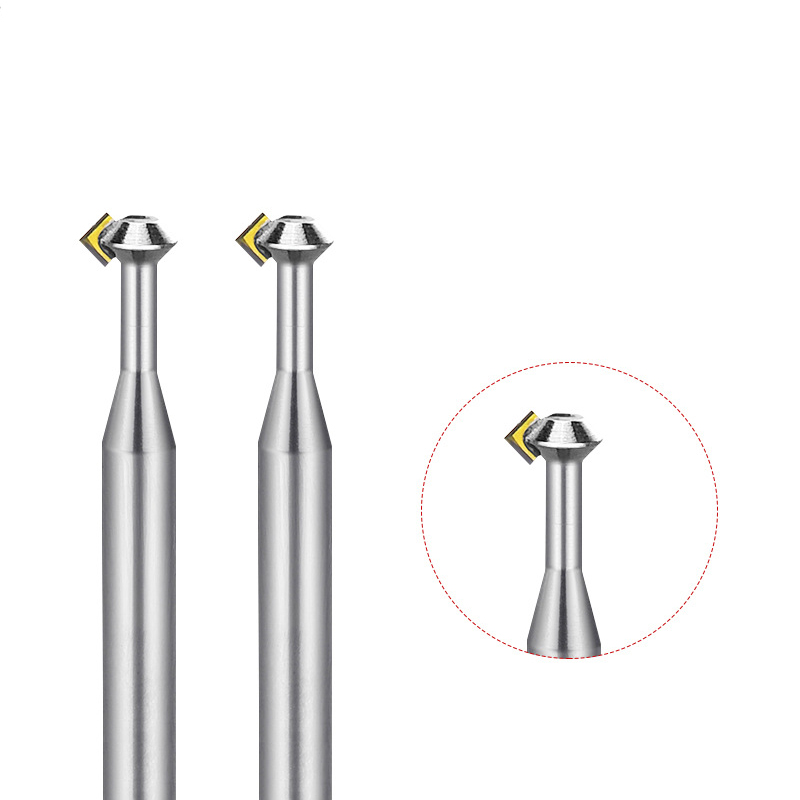
MCD High Gloss Chamfer Cutter For Gold
Product Information Origin Tianjing, China Type Flat Milling Cutter Brand Msk Whether To Coat Uncoated Series Cutter Milling Cutter Processing Range Clocks And Watches, Copp […]
Post time: 2023-07-28