Crafting a design on tool steel with an engraving machine requires meticulousness and exactitude. Machines of this kind are used to inscribe detailed patterns onto a variety of materials, with tool steel being a prime example. An engraving machine’s cutting head is either manually or electronically routed to carve out the desired pattern, as the particular design is already entered into the device’s computerized system.
Featuring the latest in computer-guided technology, the CNC machine reigns supreme as the most demanded tool for engraving into tool steel. This powerhouse is powered by a motor and controlled by a computer, providing incredible precision in three-dimensional space. This allows for intricate designs to be created, as the cutting head marches along X,Y and Z axis accurately according to its programed trajectory.
Before permitting the engraving process to commence, the tool steel must be properly prepped. This involves the cleaning of the tool steel and meticulous inspection for any vestiges of burrs or sharp edges. If deemed fitting, a file or sandpaper can be utilized to render the steel even and sleek. Following these preparatory steps, the engraving machine can proceed with the cutting activity.
When it comes to operating an engraving machine, it is pivotal to choose the appropriate end mill or router bit. This selection determines the efficiency and precision of the entire process. It is vital that the cutting tool is compatible with the engraving machine to ensure a successful outcome.
The speed of the engraving machine is essential to the quality of the final product – it must be sufficiently slow to ensure precision, yet fast enough to finish with haste. Additionally, it is vital to consider the depth of the carving: an engraving that is too shallow will lead to a feeble pattern, while a cut that is overly deep may cause too much stress on both the machine and tool.
Apart from the cutting tool and speed, how quickly the cutting head moves along the steel’s surface is equally essential. This amount of movement, referred to as the feed rate, should be calibrated precisely to suit both the tool and material being engraved.
To provide an extra layer of protection, the engraver should be kitted out with safety features like a deactivation toggle and a panic button. This will ensure that neither people nor the material being carved are put in harm’s way during the job.
After the crafting of the engraved design is accomplished, the finished result is examined for its accuracy and quality. If any mistakes have been made, then they should be addressed before sending off the steel for further processing.
A successful engraving project begins with careful preparation. Important things to consider are the type of end mill or router bit, the cutting speeds, feed rate, and safety protocols of the engraving machine. Implementing the right combination of these elements when cutting tool steel can yield a precise and efficient result.
Engraving processes involving machinery are associated with a range of industries and items. Through precise cutting of materials such as wood, plastic, and metal, intricate creations can come to life. Steel is frequently engraved with powerful tools to craft smaller components for use in a plethora of projects.
Handcrafted from an elixir of iron, carbon, and alloying elements, cutting tool steel is an ultra-durable material refined to withstand punishing temperatures and excessive pressure. This specialized steel is utilized to create the blades, cutters, and other tools essential in production. Varied grades of this iron alloy are available to match any specific application; moreover, it is often hardened for extra durability and strength.
Utilizing the high precision of an engraving machine, intricate designs and details can be cut into a variety of materials, such as cutting tool steel. These machines utilize a tool, such as a laser or rotary cutter, to carefully etch a design onto the surface of the material, creating patterns that were previously impossible to achieve. The result is a highly accurate representation that can set aside any product from its competitors.
When it comes to cutting pieces of tool steel with an engraving machine, there are several important factors that must be taken into account. Not only is it important to select the most suitable grade of steel in accordance with the size and shape of the components, but also the desired finish. In this respect, different grades necessitate varying speeds and depths during the process. Additionally, finding the correct tool for the job is essential since some tools may be more fitting for clashing with certain types of steel.
To fine-tune the cutting procedure, one must adjust the feed rate and the pressure utilized on the material. To get the most even cut, it is crucial that the feed rate matches the same rate as the tool. If thicker material or a deeper cut is desired, then a more robust pressure should be employed. Additionally, the ideal cutting fluid should be chosen to ensure that it is best suited for whatever metal is being utilized.
After the cutting has been done, the pieces can be finalized depending on the desired appearance. This could be shining, filing down, or applying paint to the components. It is also essential to take into account how precise the finish needs to be, as certain duties require more precise attention than others.
When it comes to crafting intricate parts, utilizing an engraving machine to cut tool steel is a great way to get the task done efficiently and accurately. Through collecting the optimal grade of steel and the correct cutting tool, complex components of extreme accuracy and precision can be constructed. Furthermore, with the perfect completion process, a smooth and long-lasting finish that is aesthetically pleasing can be accomplished.
Related Product
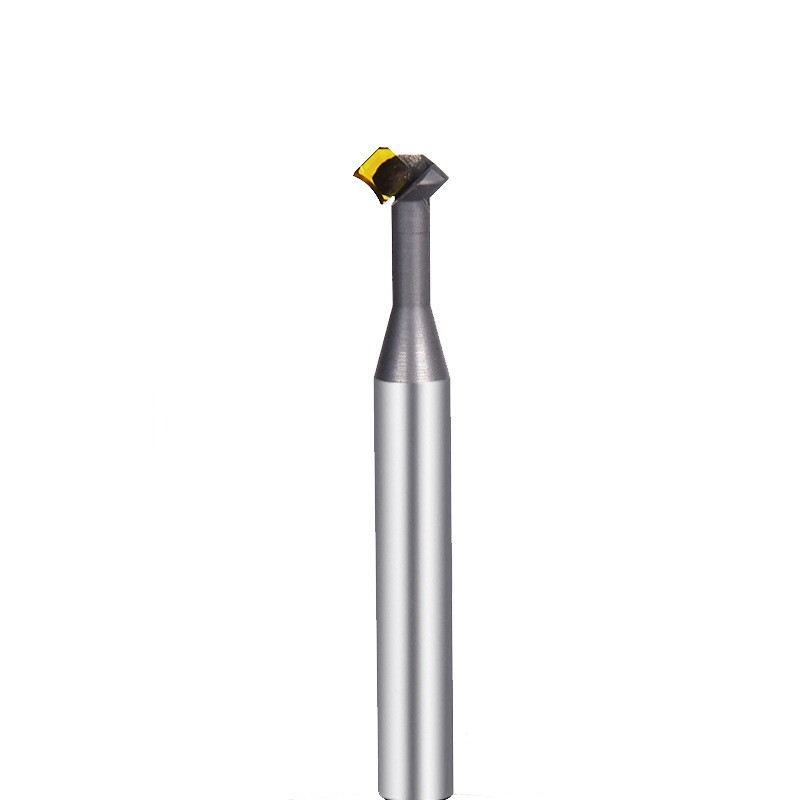
MCD Turning Tool Mirrow Finish R Cutter
Product Information Product Name Single Crystal Diamond Lower Chamfering Inner R Cutter Brand MSK Handle Material Tungsten Steel Blade Material Customized Pcd, Single Crysta […]
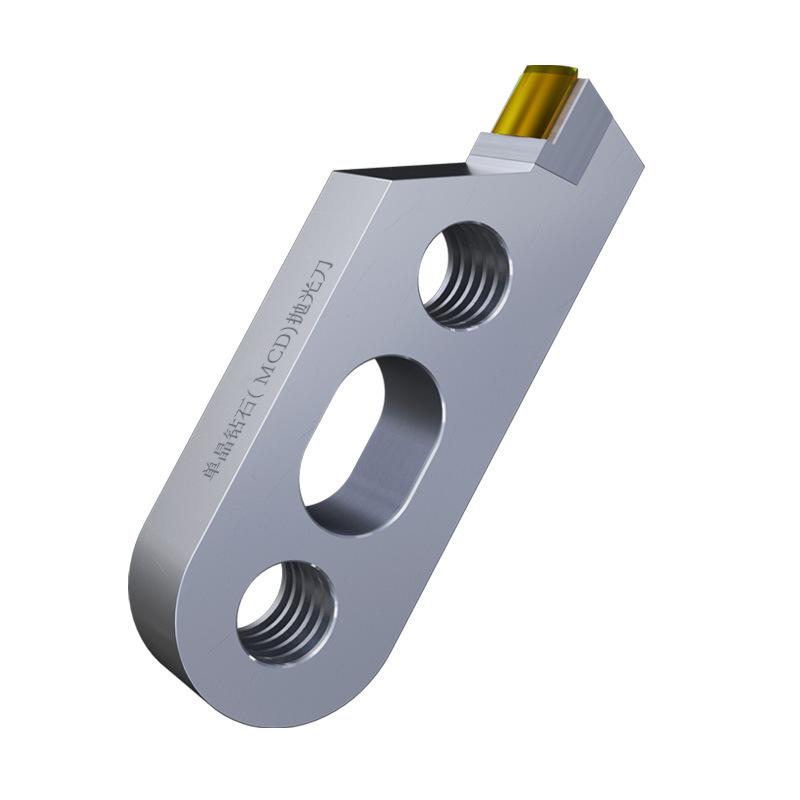
Single Crystal Diamond Polishing Cutter
Origin Tianjing, China Shank Diameter 6 (mm) Brand MSK Blade Change Method The Diamond Is Welded To The Cutter Body As A Whole Material Single Crystal Diamond (MCD) Scope Of […]
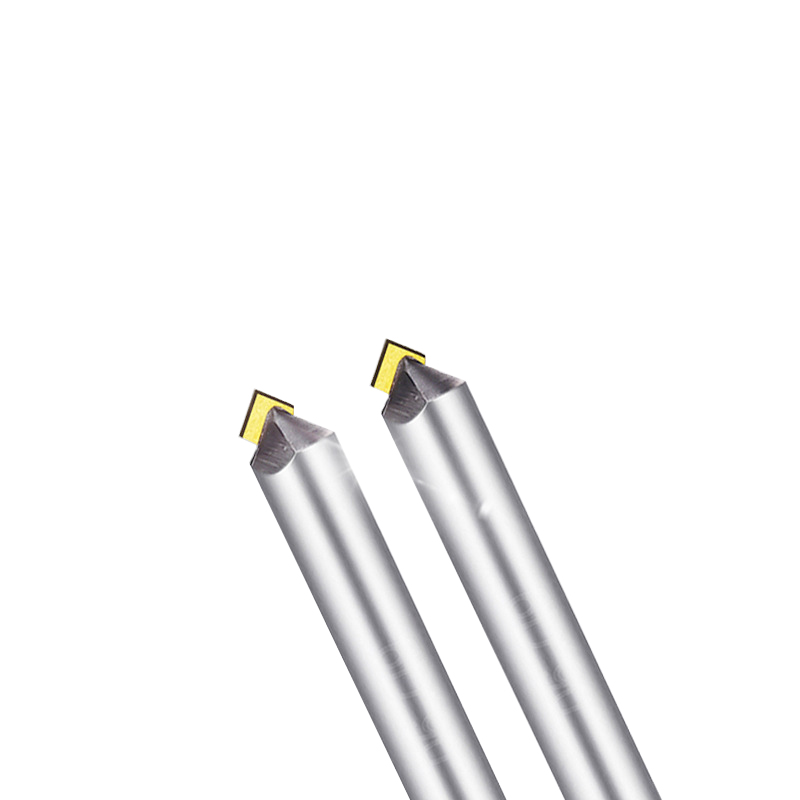
Lathe Bits MCD High Gloss Chamfer Tool
Product Information Origin Tianjing, China Cutting Edge Form Straight Edge Brand MSK Material Single Crystal Diamond Chamfer Angle 30°-180° Type Angle Milling Cutter Minimum […]
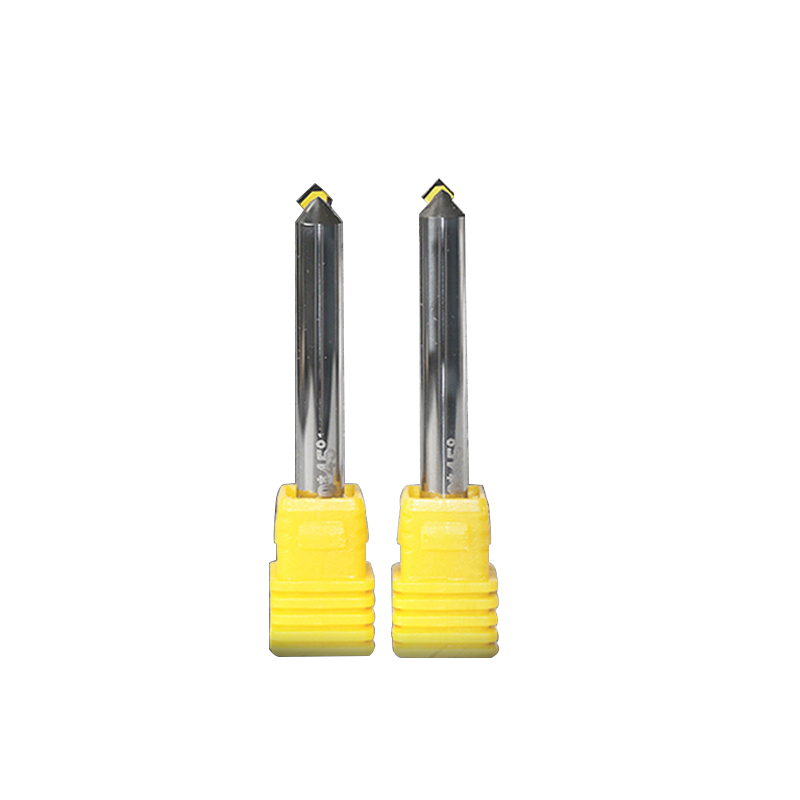
MCD Polishing Cutter for Gold Silver
Product Information Origin Tianjing, China Whether To Coat Uncoated Brand MSK Unit Weight 0.3kg Tool material Tungsten steel bar imported from Germany Product Size Shank Dia […]
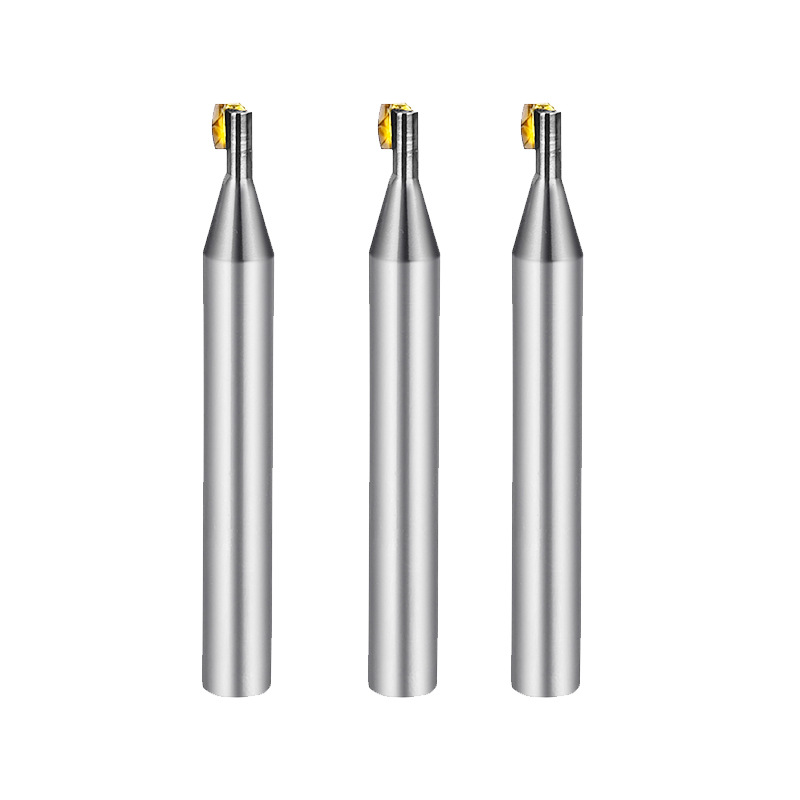
Diamond Turning Tools Outer Jewelry R Cutter
Product Information Origin Tianjing, China Material Tungsten Steel Brand Msk Type Half Round Key Milling Cutter Product Name Single Crystal Diamond Side Edge Arc Milling Cut […]
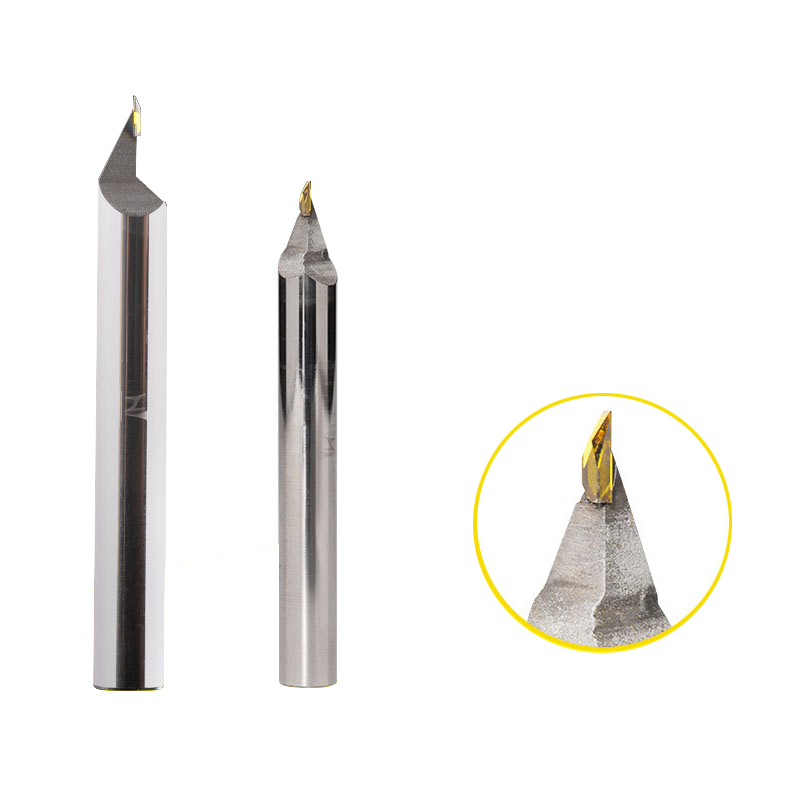
CVD/PVD/MCD Gold Jewelry Diamond Engraving Cutter
Parameter Product Name Single Crystal Diamond Carving Cutter Rotating Speed 10000-30000r/min Tool Nose Width 0.1-6.0mm Feed 1500-5000mm/min Blade Material Single Crystal Dia […]
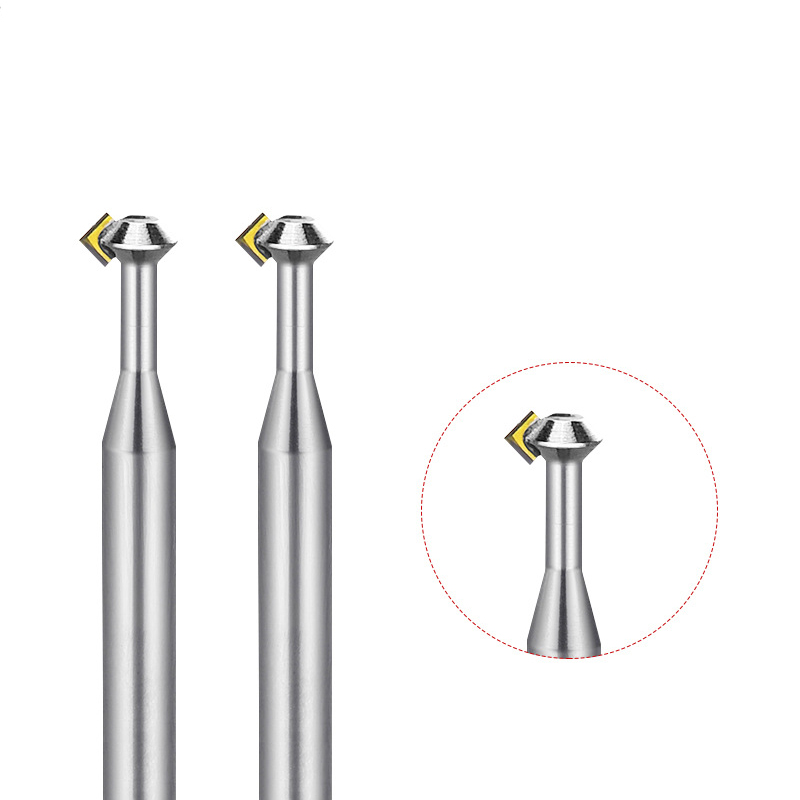
MCD High Gloss Chamfer Cutter For Gold
Product Information Origin Tianjing, China Type Flat Milling Cutter Brand Msk Whether To Coat Uncoated Series Cutter Milling Cutter Processing Range Clocks And Watches, Copp […]
Post time: 2023-07-20