(1) The single crystal diamond structure of the single crystal milling cutter is a single crystal grain, without grain boundaries and binders, so the single crystal milling cutter can not only process the high-gloss effect, but also achieve the mirror effect.
(2) It can be used to process high-hardness and difficult-to-machine workpieces, and can achieve one-time forming.
(3) Single crystal milling cutters are suitable for CNC machining centers in various fields.
(4) The single crystal milling cutter is made of single crystal diamond with high hardness and high wear resistance, which can process a mirror effect without polishing. It adopts high-quality large-grained diamond and has high durability.
(5) When using a single crystal milling cutter in a CNC machining center, choose a machine tool with high precision and low vibration, use a high speed, small cutting amount, and choose a suitable coolant to obtain a better surface finish.
The advantages of single crystal milling cutter in ultra-precision machining:
(1) The single crystal milling cutter has high hardness and high wear resistance, which can minimize the influence of tool tip wear on the size of the workpiece during ultra-precision machining.
(2) The surface roughness of the single crystal milling cutter is small, and the cutting edge is very sharp, which can reach Ra0.01~0.006μm. Therefore, it is capable of thin-layer cutting, which is beneficial to ultra-precision machining.
(3) The material friction coefficient of the single crystal milling cutter is low, and built-up edge should not be generated during cutting, so the machined surface quality is high. The surface roughness of processing non-ferrous metals can be as small as Ra0.04~0.012μm, and the processing accuracy can reach IT5 or more.
(4) The single crystal milling cutter has good thermal conductivity and low thermal expansion coefficient. Therefore, there will be no large thermal deformation during cutting, which is conducive to precision machining.
Related Product
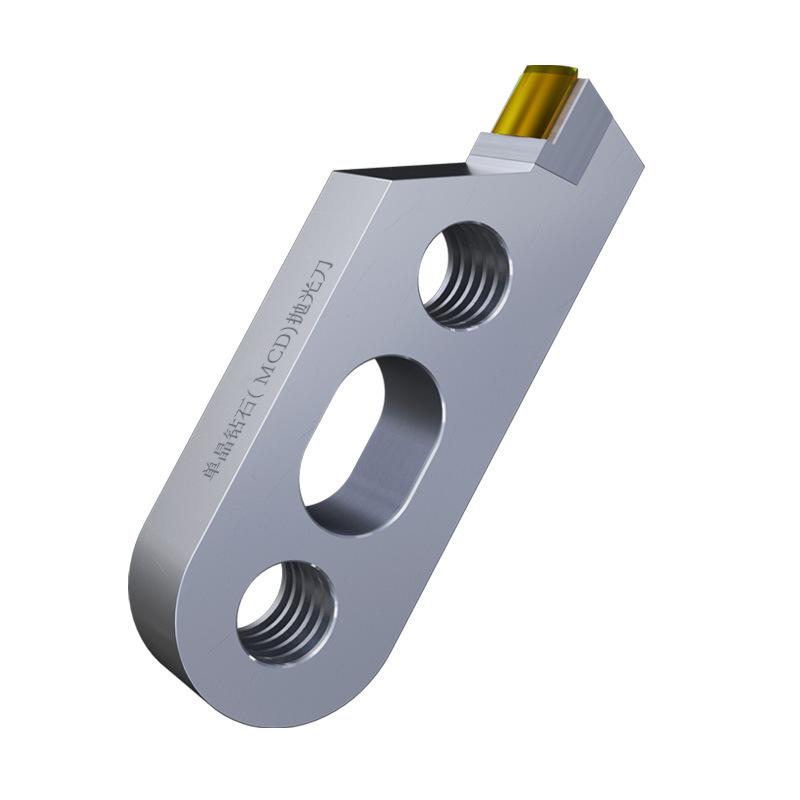
Single Crystal Diamond Polishing Cutter
Origin Tianjing, China Shank Diameter 6 (mm) Brand MSK Blade Change Method The Diamond Is Welded To The Cutter Body As A Whole Material Single Crystal Diamond (MCD) Scope Of […]
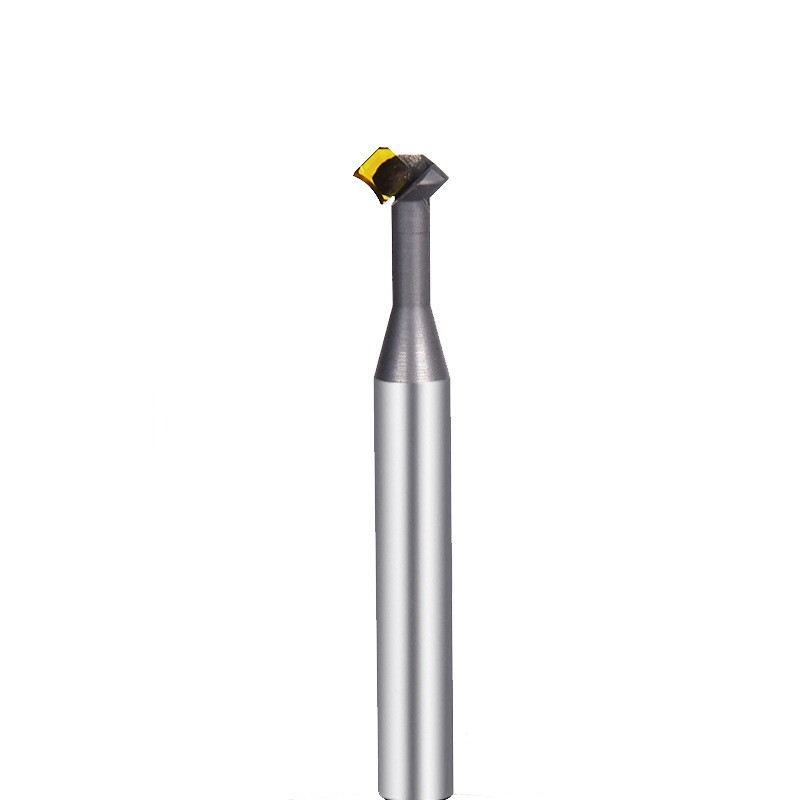
MCD Turning Tool Mirrow Finish R Cutter
Product Information Product Name Single Crystal Diamond Lower Chamfering Inner R Cutter Brand MSK Handle Material Tungsten Steel Blade Material Customized Pcd, Single Crysta […]
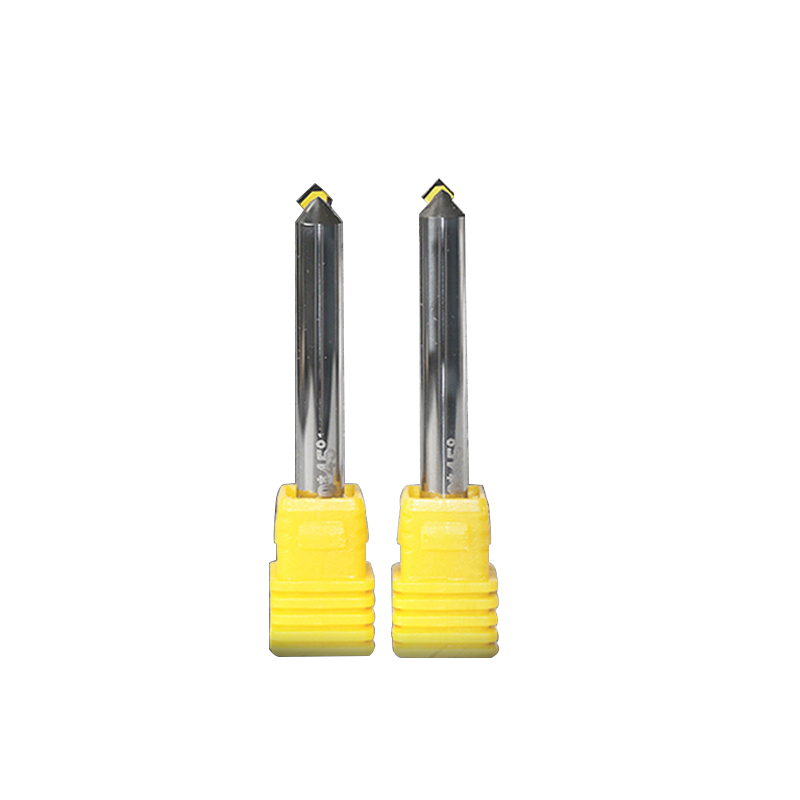
MCD Polishing Cutter for Gold Silver
Product Information Origin Tianjing, China Whether To Coat Uncoated Brand MSK Unit Weight 0.3kg Tool material Tungsten steel bar imported from Germany Product Size Shank Dia […]
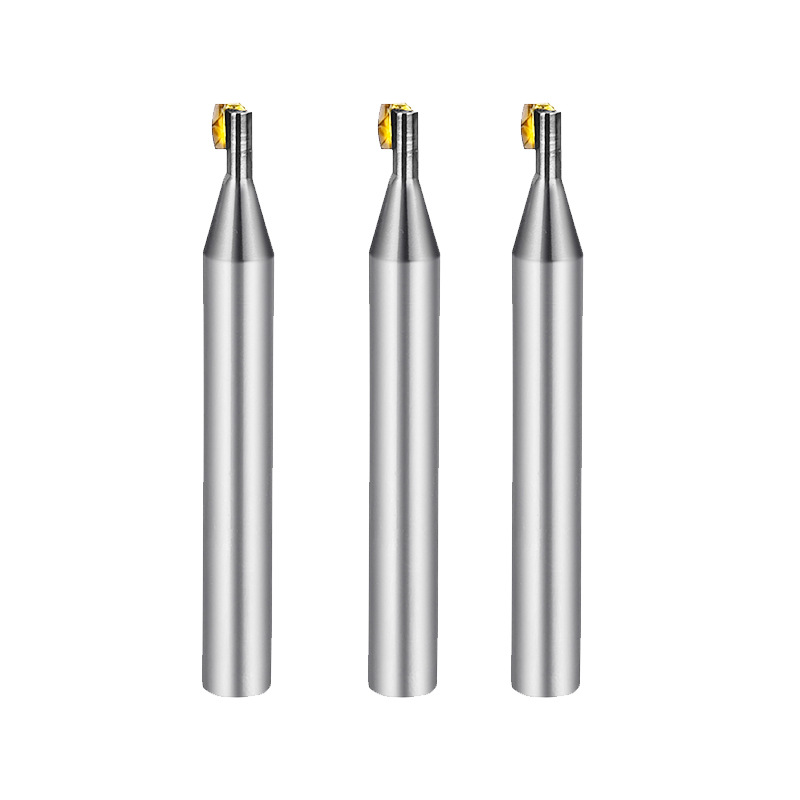
Diamond Turning Tools Outer Jewelry R Cutter
Product Information Origin Tianjing, China Material Tungsten Steel Brand Msk Type Half Round Key Milling Cutter Product Name Single Crystal Diamond Side Edge Arc Milling Cut […]
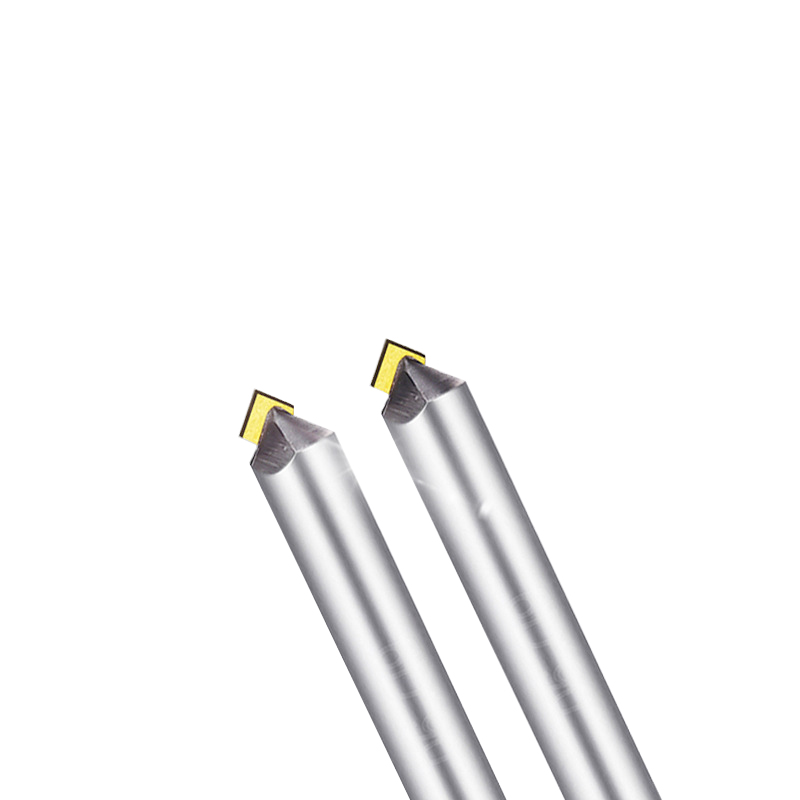
Lathe Bits MCD High Gloss Chamfer Tool
Product Information Origin Tianjing, China Cutting Edge Form Straight Edge Brand MSK Material Single Crystal Diamond Chamfer Angle 30°-180° Type Angle Milling Cutter Minimum […]
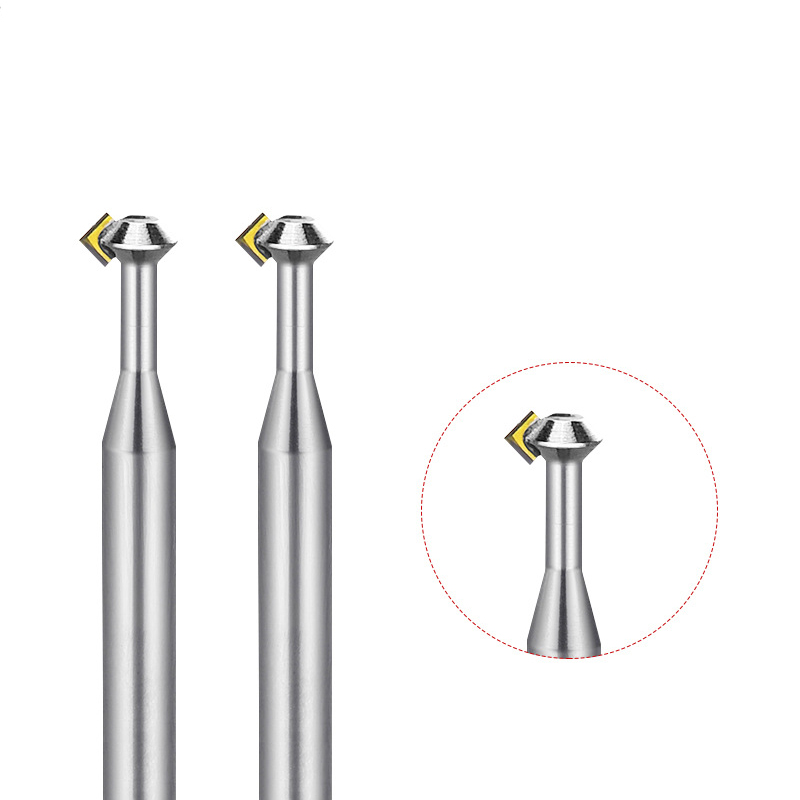
MCD High Gloss Chamfer Cutter For Gold
Product Information Origin Tianjing, China Type Flat Milling Cutter Brand Msk Whether To Coat Uncoated Series Cutter Milling Cutter Processing Range Clocks And Watches, Copp […]
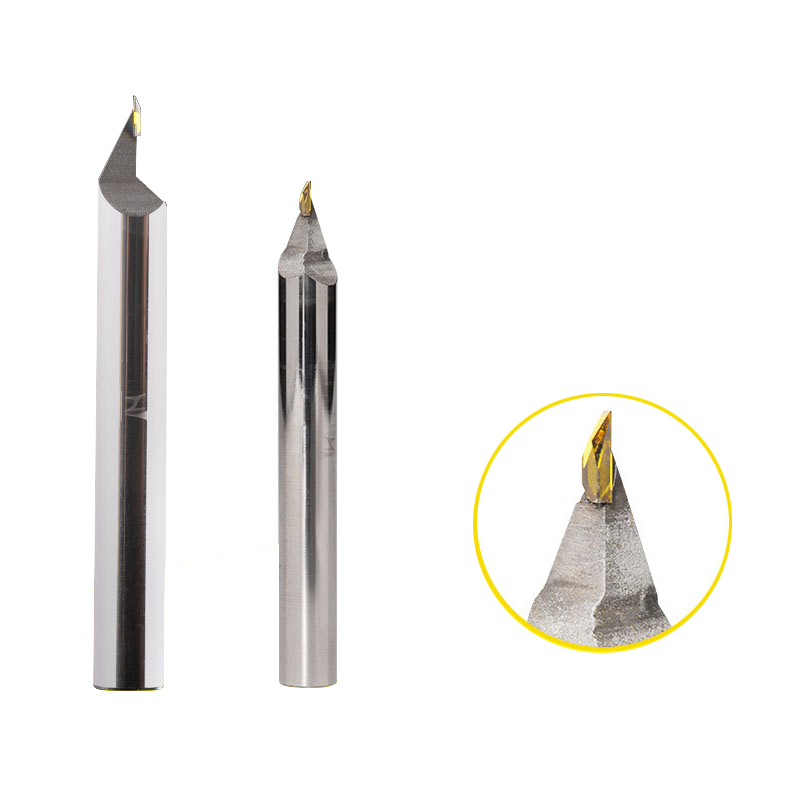
CVD/PVD/MCD Gold Jewelry Diamond Engraving Cutter
Parameter Product Name Single Crystal Diamond Carving Cutter Rotating Speed 10000-30000r/min Tool Nose Width 0.1-6.0mm Feed 1500-5000mm/min Blade Material Single Crystal Dia […]
Post time: 2022-05-17